Encoder
Encoder
Encoder is a kind of sensor, mainly used to detect the speed, position, angle, distance or count of mechanical movement. In addition to being used in industrial machinery, many motor controls such as servo motors and BLDC servo motors are required Equipped with an encoder for the motor controller to detect commutation, speed and position, so it has a wide range of applications. According to the detection principle, encoders can be divided into optical, magnetic, inductive and capacitive. According to its scale method and signal output form, it is divided into incremental encoder and absolute encoder. The photoelectric encoder uses the principle of grating diffraction to realize displacement-digital conversion. It has been applied to machine tools and computing instruments since the 1950s. Because of its simple structure, high measurement accuracy, and long life, it has received attention and promotion at home and abroad. Positioning, speed, length, acceleration, vibration and other aspects are widely used.
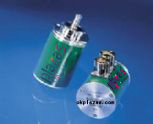
classification
Angle encoder
Angle encoders are specifically used to describe those encoders with a precision higher than ± 5” and a line count of more than 10000 lines. These devices can be used in CNC rotary tables, machine tool rotors, indexing devices, high-precision angle measuring tables, angle Precision equipment for weights and measures, antennas and telescopes, etc.
Rotary encoder
HEIDENHAIN's rotary encoder can be used as a rotary motion, angular velocity measurement sensor, and can also be used in conjunction with mechanical measurement standards, such as lead screws, to measure linear motion. Application areas include motors, machine tools, woodworking machinery, textile machinery, robots and transportation equipment, as well as various measuring, testing and inspection equipment.
Incremental angle encoders and rotary encoders determine the current position by measuring the step distance or the number of counting signals of the subdivision circuit from the origin. Heidenhain's incremental Guanshank has a reference point, and the reference point zero operation must be executed when starting up to establish the origin. The rotary encoder with commutation signal can provide the angular position of the shaft without measuring the previous movement, and its accuracy is sufficient to correctly control the phase of the rotating magnetic field of the permanent magnet three-phase motor.
Absolute angle encoders and rotary encoders can directly provide the current position value without performing the reference point return operation. Single-turn encoders can provide position values within one revolution, while multi-turn encoders can also distinguish position values from different revolutions. The measured values of HEIDENHAIN's absolute angle encoders and rotary encoders are transmitted via EnDat, SSI, PROFIBUS-DP or other serial data interfaces. EnDat or PROFIBUS-DP bidirectional interface supports high-level automatic configuration of the circuit, and has detection and diagnosis functions. Using programmable rotary encoders, users can adjust the functions and parameters of different encoders through the software on the computer.
Magnetic encoder
The excellent performance ERM magnetic encoder is especially suitable for production equipment. The large inner diameter and compact scanning head make them more effective in:
C axis of lathe
Stator orientation of milling machine
auxiliary axis
gear set
The signal period of about 400 μm and the special MAGNODUR grating application process enable the accuracy and shaft speed to meet the requirements of the above-mentioned applications.
structure
Encoder is mainly composed of code disc (circular grating, indicating grating), body, light-emitting device, photosensitive device and other components.
(1) The circular grating is composed of radial stripes of light and dark painted on a transparent material or a metal material. The pitch of an adjacent fringe is called a grid section, and the number of grid sections in the entire circumference of the grating is the pulse number (resolution) of the encoder. (Note: There are three kinds of code plates in our company: metal, glass, and film (similar to plastic)).
(2) It indicates that the grating is a fixed piece of grating, but the grating strips of the window fringe are exactly the same as the grating fringe of the circular grating.
(3) The body is a carrier for assembling circular gratings, indicating gratings and other components.
(4) The light-emitting device is generally an infrared light-emitting tube.
(5) The photosensitive device is a high-frequency photosensitive element; generally there are silicon photocells and photosensitive triodes.
working principle
A pair of scanning systems is composed of a circular grating and an indicating grating. A beam of infrared light is projected on one side of the scanning system, and the photosensitive device on the other side of the scanning system can receive the scanning light signal; when the circular grating rotates, the photosensitive device The received scanning light signal will change, and the photosensitive device can convert the light signal into an electrical signal and output it to the control system or instrument.
Generally, the output signal of the encoder is two columns of Sin signal and Cos signal with a 90 degree phase difference (this is guaranteed by the grating's window fringe reticle); the period of these signals is equal to the rotation of the circular grating through one grid section (P) In the moving time, a square wave pulse signal can be output by amplifying and shaping the Sin signal and Cos signal.
Application occasion
Encoders are mainly used in CNC machine tools and mechanical accessories, robots, automatic assembly machines, automatic production lines, elevators, textile machinery, sewing machinery, packaging machinery (fixed length), printing machinery (synchronous), woodworking machinery, plastic machinery (fixed number) , Rubber and plastic machinery, drawing instruments, goniometers, convalescent radars, etc.