Encoder2021
Encoder2021
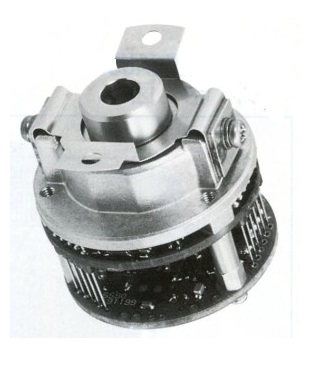
In the industrial field, an encoder refers to a sensor device that converts displacement into a digital signal. Encoders are used to detect the speed, position, angle, distance or count of mechanical movement, and convert angular displacement or linear displacement into electrical signals. Encoders, especially rotary encoders, are widely used in machine tools, material processing, motor feedback systems, and measurement and control equipment. For example, servo motors need to be equipped with encoders to achieve commutation, speed and position detection.
There are many kinds of encoders. According to their scale method and signal output principle, they can be divided into three types: incremental encoder, absolute encoder, and hybrid. For absolute encoders, it can be subdivided into single-turn absolute encoders. And multi-turn absolute encoder.
According to the detection principle, encoders can be divided into photoelectric encoders, magnetic encoders, and inductive and capacitive.
According to the installation form of the encoder, it can be divided into solid shaft and hollow shaft. The hollow shaft can be subdivided into sleeve type and through-hole shaft.
According to the use environment of the encoder, it can be divided into industrial load type, heavy load type and explosion-proof type.
The characteristics of commonly used different types of encoders:
Incremental encoder
Advantages: The principle structure is simple, the average mechanical life can be more than tens of thousands of hours, the reliability is high, and it is suitable for long-distance transmission.
Disadvantages: Only the relative position can be output, the absolute position of the shaft cannot be output, and the data is lost when the power is turned off.
Absolute encoder
Advantages: no need to remember, no need to find a reference point, anti-interference characteristics, data reliability, higher resolution, fast start-up speed, accurate multi-axis motion control, multiple communication protocols.
Disadvantages: The installation and debugging is difficult.
Photoelectric encoder
Advantages: small size, precision, high resolution, no contact and no wear; long life, easy installation, rich interface forms, and reasonable price. The same type can detect both angular displacement and linear displacement with the help of a mechanical conversion device; the multi-turn photoelectric absolute encoder can detect linear displacement with a long range.
Disadvantages: higher protection requirements are put forward for outdoor and harsh environments; the measurement of linear displacement needs to rely on mechanical device conversion, and the error caused by mechanical gaps needs to be eliminated; detection of orbital objects is easy to cause slip.
Magnetic encoder
Advantages: simple structure, resistance to harsh environments, wide response frequency, easy to achieve absolute position output, and lower cost.
Disadvantages: The accuracy requirements cannot be too high.
Hollow shaft encoder
It is compact, easy to adjust, and adapts to a variety of applications. The shaft diameter of the hollow shaft encoder is adapted to the extended shaft of the motor, and the position can be flexibly adjusted by the spring sheet. No additional parts are required during installation, which leads to an increase in installation size. It is convenient to adjust the position and absorb the vibration and shock of the load.
Solid shaft encoder
An elastic coupling is required when installing, and the operation of a solid shaft encoder requires relatively high shaft alignment accuracy.