How to choose a suitable encoder according to motor parameters?
How to choose a suitable encoder according to motor parameters?
How to choose a suitable encoder according to motor parameters?
When the motor motion control system needs to select an encoder, it will face many technical terms, and the amount of available data may be very large. Three important concepts worth noting: resolution, precision, and precision. These terms are independent of each other. Each of them refers to a specific encoder characteristic. They are not interchangeable. Any specific type of encoder can be used within a certain resolution range. For example, an encoder may have more than 10 different resolutions, ranging from 64 CPR to 10,000 CPR.
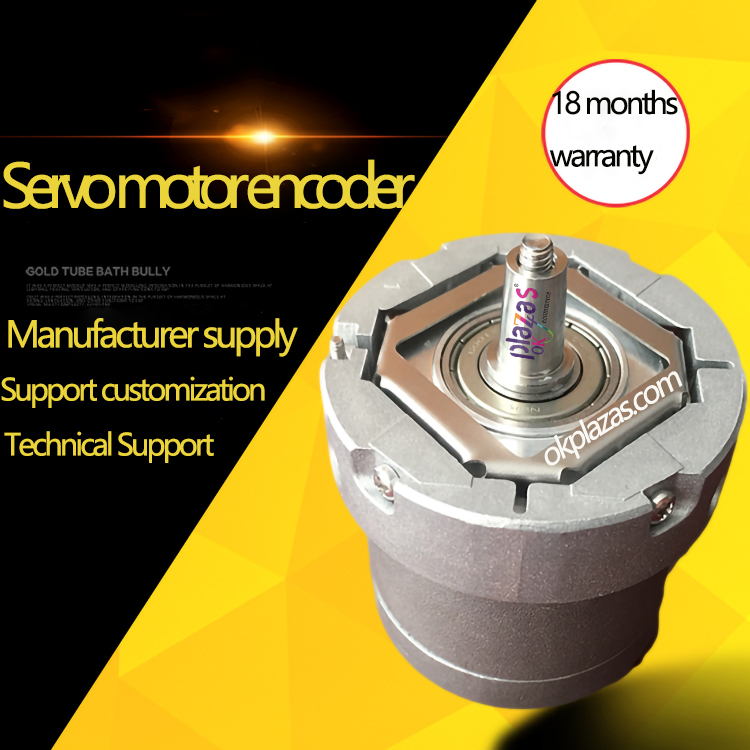
With the development of technology, encoders are widely used in the industrial control industry
What parameters should be paid attention to when choosing an encoder:
1. Resolution (number of pulses), that is, the number of pulses output per revolution when the encoder is working, whether it meets the design and use accuracy requirements.
2. Installation dimensions, including positioning stop, installation hole position, shaft diameter, cable outlet method, installation space volume, and whether the working environment protection level meets the requirements. (See product manual when choosing)
3.Electrical interface, encoder output methods commonly include push-pull output (F type HTL format), voltage output (V), open collector (N, NPN type output), long-line driver output (C differential output). Its output mode should match the interface circuit of its control system.
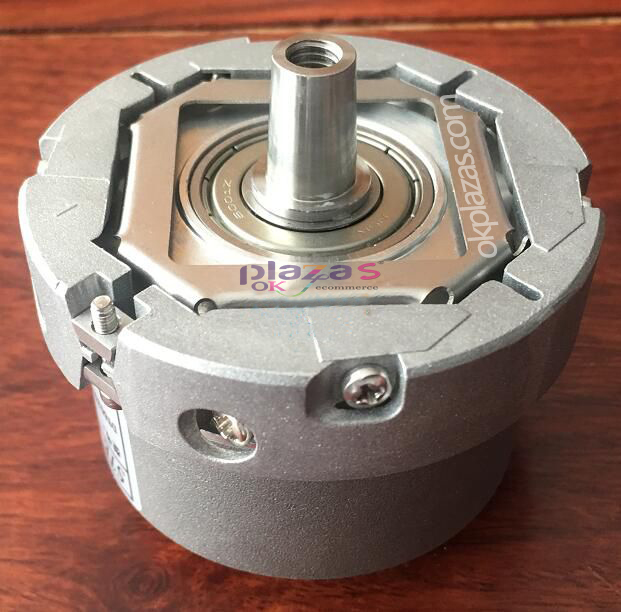
How to choose a suitable encoder according to different motor parameters?
1 Motor and mechanical appearance style.
2 Mechanical speed (Speed)-the structural design of the encoder makes it the maximum rotational speed that it can reach and withstand, which is expressed as the rotational speed that can be achieved within one minute-rpm; (so the maximum working speed of the encoder should be considered at the same time The mechanical speed and response frequency of the encoder and the switching frequency of the subsequent receiving device of the encoder).
3 Shaft Dimension—The shaft diameter of the solid shaft of the encoder is 6 mm*, 8 mm, 10 mm*, 12 mm, etc., and the shaft diameter of the hollow shaft is 8 mm, 10 mm, 12 mm*, large diameter 20 ~50mm* etc., the ones with * are conventional specifications.
4 Resolution (Resolution)—The number of signals output per revolution of the encoder in a single revolution is called resolution, also called resolution, or directly called the number of lines. Generally, the number of encoder output lines is 5~10000 lines . Such as: 1024ppr, 2048ppr, etc.
5 Power-Vcc—Encoders generally have only two voltages, one is DC9~36V, and the other is DC5V standard voltage.
6 Working temperature (Temperature)—The highest and lowest working temperature of the encoder represents the internal mechanical [coordination and composition of the encoder, as well as the level of electronic components. The better working temperature of the encoder is from -40 to 100°C. In fact, under low temperature conditions, the internal electronic parts and external cables and sealing characteristics are restricted.
7 The degree of protection of the motor.