Inclination sensor aerial operating vehicle industry application
Inclination sensor aerial operating vehicle industry application
Inclination sensor aerial operating vehicle industry application
Ground equipment such as road signs, wiring hubs, and base stations is an indispensable device in people's daily life. In the past, maintenance, replacement, and cleaning of road signs used slides and loaders to work, which is inconvenient and has potential safety hazards. In order to solve this practical problem, the Qingyuan County Highway Administration Bureau of Zhejiang Province recently purchased an inclination sensor aerial work vehicle with a high-pressure cleaning function, which is convenient for the maintenance, replacement and cleaning of signs and signs, and can also solve the maintenance of tunnel lights. Difficulty in working at heights. The high-altitude operating vehicle uses multiple inclination sensors to detect the inclination to ensure the safety of workers.
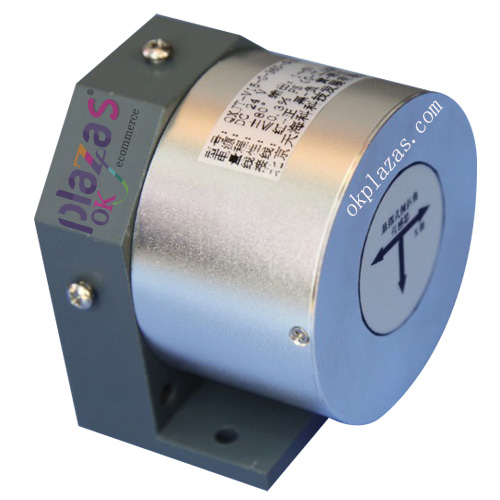
The live working vehicle slowly stopped beside a 10-kV utility pole in front of a factory, and two live working workers got on the cart. Immediately afterwards, two live workers worked together and one operated the bucket arm to raise the bucket to an altitude of nearly 10 meters above the ground. With the economic and social development of our county, the requirements for electric power construction are getting higher and higher. In the past, "highly difficult" live work has become a "routine project." In order to replace the load switch, it is a relatively simple project, and an aerial work truck is required.
The tilt switch is used to detect whether the vehicle body is tilted, and the tilt sensor detects the tilt of the forearm of the aerial work vehicle. The accuracy of the detection is closely related to the quality of the tilt sensor itself. This type of industry also uses limit switches, toggle switches, and hour meters.
The core part of the tilt sensor is the symmetrical capacitor block of the micromechanical acceleration sensor element, which is composed of three silicon wafers separated from each other by a thin glass film. The middle silicon chip is a cantilever multi-ray structure, and the large mass on it, the capacitance and the elastic coefficient can independently obtain the best results. This is the reason for obtaining good measurement results in the low g range. The force of gravity and acceleration acting on the silicon wafer causes the monocrystalline silicon electric beam to oscillate and bend. This deviation can be measured by the change in the distance between the capacitance of the two metal films as electrodes. The micro-mechanical sheet can easily detect relatively large capacitance and capacitance changes.