Interpretation the true face of the smart factory needed by the fourth industrial revolution
Interpretation the true face of the smart factory needed by the fourth industrial revolution
Interpretation the true face of the smart factory needed by the fourth industrial revolution
Interpretation: the true face of the smart factory needed by the fourth industrial revolution
Relying on the combination of cyber-physical system (CPS) and information and communication technology, the factory will introduce big data technology for analysis and optimization management. In a computer virtual environment, the entire production process will be simulated, evaluated and optimized, and finally automation, intelligence, and Interconnected manufacturing.
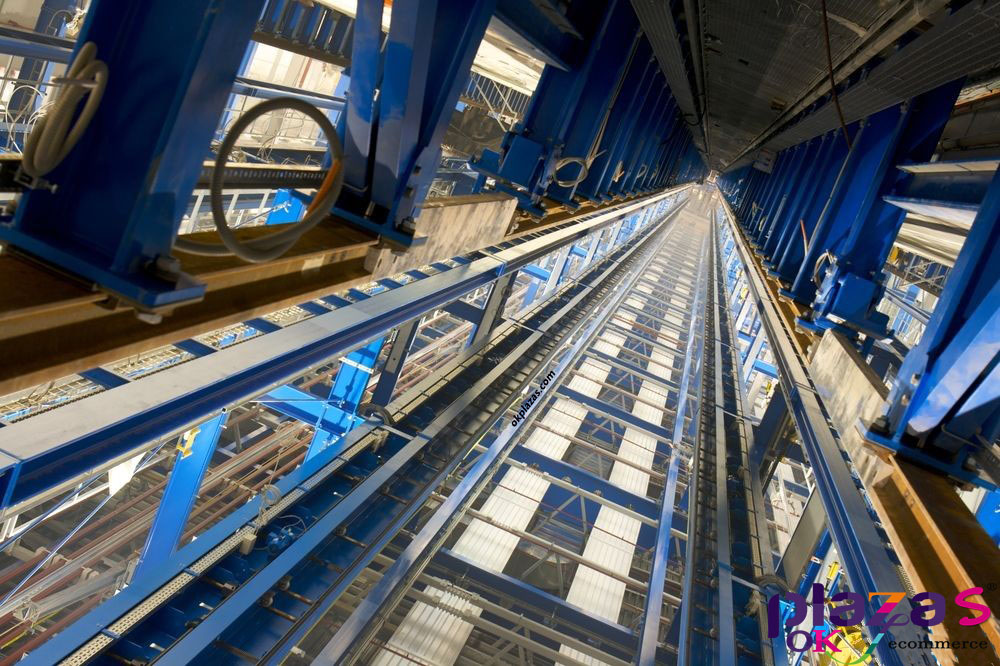
Interpretation the true face of the smart factory needed by the fourth industrial revolution
Interpretation: the true face of the smart factory needed by the fourth industrial revolution
Relying on the combination of cyber-physical system (CPS) and information and communication technology, the factory will introduce big data technology for analysis and optimization management. In a computer virtual environment, the entire production process will be simulated, evaluated and optimized, and finally automation, intelligence, and Interconnected manufacturing.
图
In the German concept, a factory that can realize this manufacturing method is called a smart factory. One of the development directions of the Industry 4.0 strategy is the smart factory. In this new revolution, automakers, component suppliers, software providers, etc. have their own interpretations of smart factories from the perspective of their own needs, and thus bring different levels of practice and different forms of intelligence. Manufacturing solutions.
The automotive industry is the most widely used field of robots. The high degree of automation in automobile manufacturing makes robots appear more and more in factories. However, this is not enough. The era of interconnection puts forward higher requirements for industrial manufacturing. Automated factories are further upgraded, adding the concept of interconnection: connecting factory machines and people to the network, between machines and machines, between people and machines. To achieve a dialogue between.
From manufacturing to "smart manufacturing"
is widely used in automation, digitization, and intelligent workshops in the automotive industry, and has become an important carrier of automotive intelligent manufacturing. Here, you can see fewer and fewer workers, replaced by intelligent robots with higher efficiency and accuracy, and more and more key processes have been replaced by robots. In recent years, "unmanned" workshops have emerged. Complex operations such as arc welding, spot welding, assembly, handling, painting, inspection, palletizing, grinding and polishing, and laser processing are all handed over to industrial robots to make a conveyor belt. Different types of robots have a clear division of labor and are lined up on both sides. In just one minute, a complete car is "born" in the robot's "crash".
In my country, industrial robots were originally mainly used for spraying and welding of automobiles and construction machinery. With the continuous growth of automobile demand, industrial robots have been widely involved in the four major processes of automobile production and the production of key automobile parts. In the production of automobile bodies, there are a large number of applications such as die-casting, welding, and testing. These are currently completed by industrial robots. In particular, welding robots on the welding line play an irreplaceable role in the automobile manufacturing industry. Welding robots are advanced welding equipment developed on the basis of industrial robots. They are industrial robots engaged in welding (including cutting and spraying). They are mainly used in the field of industrial automation. They are widely used in automobile and parts manufacturing, motorcycles, engineering Machinery and other industries are widely used in the four major production processes of automobile production: stamping, welding, painting, and final assembly, of which arc welding and spot welding are the most widely used. Compared with manual welding, the use of robot welding has three advantages: stable quality, greatly increased efficiency, and more safety.
In the production of automotive interior parts, skin weakening robots, foaming robots, and final product cutting robots are required. Due to the heavy workload and high risk of spraying on car bodies, industrial robots are usually used instead. In recent years, to adapt to the development trend of flexible, agile, intelligent and informatized modern automobile manufacturing technology, the domestic automobile manufacturing industry has introduced AGV (also known as mobile robot) technology in automobile production, so that the production organization of automobile assembly, A qualitative leap has been achieved in information management and logistics technology.
Changes in foreign parts factories
On a hydraulic product production line at the Bosch Humboldt factory in Germany, all parts are equipped with a unique radio frequency identification code (RHD) and can automatically talk to checkpoints along the way. When the workpiece arrives at a certain station, the display will respond accordingly It reminds employees of the specific work content they need to handle, and each workstation can also be automatically adjusted according to the employee's personalized settings.
Bosch has applied Industry 4.0 concepts and technologies in more than 250 factories around the world. Its factory in Suzhou, China is also one of its Industry 4.0 pilot bases, where everything from basic paperless office to the implementation of automatic material preparation systems has been- -Become reality. In the future Bosch factory, a video image of a tablet computer will give comprehensive information and maintenance instructions for the displayed parts, and workers can process this information directly through the touch screen.
Interpretation: The true face of the smart factory needed by the fourth industrial revolution (picture from Baidu picture)
And Heinrich Hiesitiger, chairman of the board of directors of the German ThyssenKrupp Group, believes that the implementation of the Industry 4.0 concept requires a lot of preparatory work. For example, IT infrastructure must be prepared, network speed must be guaranteed, and these new infrastructures must also be integrated into existing production facilities to ensure efficient methods to transmit and transmit large amounts of information and data.
Now, ThyssenKrupp Group hopes to connect IT networks in more than 2,300 different locations through high-speed and ultra-wide bandwidth infrastructure. Another important prerequisite is the automation of production facilities. In November 2014, ThyssenKrupp Engine Systems (Changzhou) Co., Ltd. officially opened. This engine system production base will produce engine cylinder head cover module assemblies in China.
The customer sends the required steel plate information to ThyssenKrupp through the electronic order system. The information and data will be transmitted to the production company immediately, and the relevant information and data during production will be entered into the sap system. In this way, a steel plate has been given an electronic code during the production process, which contains complete product information.
In the entire production process, customers can know the status of all steel plates in real time, and can also change some sequences or some production requirements. Just tell ThyssenKrupp 8 hours before the steel plate is put into production, and you can make changes immediately. At present, this process has been implemented in a factory in Germany.
OEM's response
Industry 4.0 is not a sudden revolution, nor an innovation that can be achieved overnight. The BMW Group Industry 4.0 production expert, Dr. Christian Patron, believes that “in the BMW Group, continuous improvement of the production system is a daily work, and Industry 4.0 is the next step in line with BMW’s logic, not a revolutionary change”.
Some attempts at the automation and intelligence of BMW factories have been listed as production methods of Industry 4.0. A widely mentioned example is the use of non-contact gesture recognition systems in the production of car bumpers at the BMW Landshut plant. This system is regarded as an example of intelligent human-computer interaction. The virtual gesture recognition system is composed of two 3D cameras and infrared sensors installed above the inspection work area. The 3D physical model data of the bumper components are stored in the system, and a 3D spatial scanning coordinate system is established in the inspection area. When the workpiece enters the inspection area, the inspector only needs a few gestures to complete the inspection work: for example, after pointing the position of the deviation, the device can accurately record the position of the deviation and the deviation data; and if the part is qualified, The inspector only needs to slide his finger to indicate to the system that the part has passed the inspection.
With the support of this innovative system, not only can it speed up the inspection process. The positioning accuracy of inspection accuracy and part deviation is also greatly improved. At the same time, because there is no need to be equipped with goggles, microphones and other equipment, it improves the comfort and efficiency of the inspector's work. In addition, the system is simple and easy to learn, which is highly recognized and welcomed by the inspectors.
This just confirms the statement of the new chairman of the BMW Group, Harald Kmger-"For BMW, Industry 4.0 is not a blind pursuit of automation and the exclusion of people from participating in the entire production process; on the contrary, we believe that the future of intelligence Science and technology will focus on the higher level of human-computer interaction, so that technology equipment can provide better support for staff."
On May 22, Audi interpreted the vision of "Smart Factory" through the "Encounter" magazine at the company's annual shareholders meeting. In their plan, one day, the automobile factory will have a completely different intelligent system, innovative technology, and efficient organizational structure. In their planning, assembly lines no longer exist, and orderly flow operations are no longer applicable. Flatbed transportation robots-the so-called "Driverless Transport Systems" (DriverlessTransportSystems) "handles" various unfinished cars. In this factory, you will see all Audi models, but you can't find two complete cars The same car. Audi has set a cut-off point for the transformation of this scene into reality-2030.
Compared with German car companies such as BMW, Japanese car company Toyota also has its own mature manufacturing system. Although Japan did not propose a concept similar to Industry 4.0, Toyota has expanded on the basis of lean production created in the 1960s. To a certain extent, there are many integrations with the Industry 4.0 concept released in the 21st century.
dual role
In the process of advancing Industry 4.0, data security is an item of great concern to enterprises. Infineon and Deutsche Telekom jointly launched a security solution for protecting networked production.
At the 1T summit in Germany last year, German Chancellor Merkel watched the Industry 4.0 smart production demonstration. Infineon’s security products authenticated each link of production to ensure data and information security throughout the production process. Practice Industry 4.0 in the factory and provide solutions for other companies. In the advancement of Industry 4.0, Infineon has actually played a dual role.
Also playing a dual role are giants such as Bosch and Siemens. They have also launched their own smart manufacturing solutions based on their respective advantages: Siemens believes that the future combination of the Internet and traditional manufacturing will be implemented in digital factories, so it launched its own Digital Factory Solutions (DigitalFactorySoluticm). To this end, Siemens acquired PLM software vendor UGS in 2006 for US$3.2 billion.
UCS has an online design software platform NX, which includes a series of design software such as CAD and CAM, as well as digital production process planning software and leading solutions on the market. Siemens integrated the UGS software platform into its own industrial automated production system to form a set of manufacturing solutions. After the integration, the Siemens digital factory blueprint has begun to take shape. Based on a data sharing cooperation platform, producers, users, and suppliers form a digital factory. Through the three-in-one software system platform of PLM, MES, and TIA, real-time communication is achieved to achieve product development and design Full-cycle management to after-sales service.
On the digital simulation platform, there is a one-to-one correspondence between virtual products and real products that go through the process in the factory. The specific execution system in the factory can be reconstructed to a certain extent according to the requirements of the digital simulation platform. At present, Siemens' digital factory solutions have been applied in the automated manufacturing processes of some high-end automotive industries. In addition, in order to cooperate with its own industrial automation products, Siemens also launched a "Siemens Industry Support Center" APP. This APP integrates more than 5,000 Siemens manuals, operating instructions, and more than 60,000 FAQs into the network platform, which provides great convenience to customers.
Bosch has also been studying solutions for Industry 4.0, and recently launched the "Huilian Manufacturing" solution. The core of the program is a manufacturing logistics software platform, including process quality management, remote service management, and predictive maintenance.
Some people believe that in this plan, process quality management already has the basic elements of smart factories such as real-time interconnection of information in the factory. Remote service management and predictive maintenance are all based on the value chain extension generated by the Internet of Things, which means that Bosch’s wisdom Even manufacturing already has the key foundation of Industry 4.0.