Introduction to the related principles and application knowledge of absolute encoders and incremental encoders
Introduction to the related principles and application knowledge of absolute encoders and incremental encoders
Introduction to the related principles and application knowledge of absolute encoders and incremental encoders
Introduction to the related principles and application knowledge of absolute encoders and incremental encoders
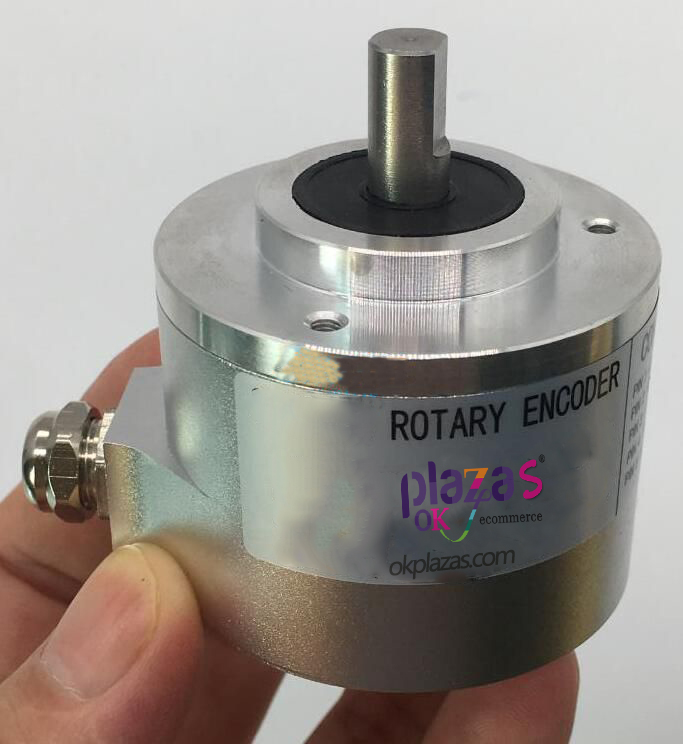
With the development and change of technology, encoders are widely used in various industries. There are many types of encoders, and there are also many types of output signal forms. At present, the photoelectric encoder is mainly used, and the output signal form is pulse mode. For example, the code disc of the photoelectric encoder is installed on the motor shaft, and there are ring-shaped, dark engraved lines on it. Through the LED emitting light source, the matrix arrangement of multiple groups of optocoupler devices improves the signal stability, and by receiving the strength of the light source, the internal comparison outputs the A and B signals. The A and B signals are 90 degrees out of phase. In addition, a Z-phase pulse is output every revolution to represent the zero reference position.
Since the phase A and B are different by 90 degrees, the forward and reverse rotation of the encoder can be judged by comparing whether the A phase is the first or the B phase is the first. In order to increase the stability of the encoder signal long-line transmission, the A, B, and Z signals are output differentially to increase the signal stability. The Hall signals U, V and W of the photoelectric encoder are basically the same as the A and B signals. Brushless or low-voltage servos also generate Hall signals through magnetic rings and Hall elements.
Encoders are widely used. In today's elevator drive control, in order to obtain the precise speed of the traction motor of the elevator and the precise position of the elevator car in the hoistway. It meets the digital operation of the frequency converter's central processing unit for precise control of the speed setting and feedback, the precise position control of the elevator car, and the precise grasp of the acceleration and deceleration poles and stopping.
Principle characteristics of incremental rotary encoder
Incremental rotary encoders output pulses during rotation, determine the direction through the phases of A and B phases, and use counting equipment to know its position. When the encoder does not move or power is off, the internal memory of the counting equipment is used to remember position. In this way, when the power is off, the encoder cannot move. When the power is on, the encoder cannot lose the pulse due to interference during the pulse output. Otherwise, the zero point of the counting device will shift, and this deviation There is no way to know the amount of shift, only after the wrong production results appear.
The difference between absolute encoder and incremental encoder
Absolute encoders differ from incremental encoders in the gap pattern of the rotating code disc, and their characteristics are different from incremental encoders: absolute encoders are significantly better than incremental encoders in terms of positioning. Direct output position, which is beyond the reach of incremental encoders. The absolute encoder does not need to determine the direction, and automatically recognizes it during operation.
Introduction to the related principles and application knowledge of absolute encoders and incremental encoders
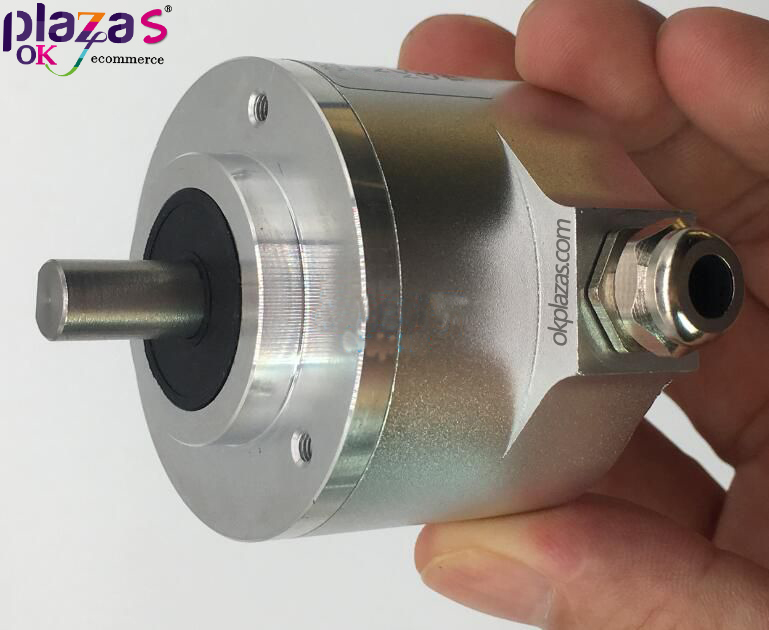
There are many engraved lines on the optical code disc of absolute encoder, and each engraved line is arranged in order of 2, 4, 8 and 16 lines. In this way, at each position of the encoder, by reading the open and dark of each engraved line, a set of unique binary codes (Gray codes) from the zero power of 2 to the n-1 power of 2 are obtained. This is called an n-bit absolute encoder. Such an encoder is determined by the mechanical position of the encoder, and it is not affected by power outage interference.
The single-turn absolute encoder can make a full 360-degree rotation. After the device is powered off, it can accurately determine its position after power supply. When the rotation is greater than 360 degrees, a multi-turn absolute encoder must be used. The multi-turn rotary encoder will run more than one revolution. On the basis of the rotation, it is transmitted to another code disc through a gear transmission to increase the The number of pole turns to achieve. Enlarging the measuring position range of the encoder, the code is determined by the mechanical position, and each position code is unique and does not repeat, without memory. The output of absolute encoder is multi-bit pulse digital (Gray code or pure binary code) output. The purchase price is almost the same when used.