Multiple applications of Pepperl+Fuchs sensor cables
Multiple applications of Pepperl+Fuchs sensor cables
Keywords: photoelectric switch photoelectric switch manufacturer photoelectric switch model photoelectric switch price photoelectric switch wiring diagram photoelectric switch principle photoelectric switch type photoelectric switch application
Photoelectric switch:
The photoelectric switch is the abbreviation of the photoelectric proximity switch. It utilizes the shielding or reflection of the light beam by the detected object, and the circuit is connected by the synchronization loop to detect the presence or absence of the object. Objects are not limited to metal, all objects that can reflect light (or block light) can be detected. The photoelectric switch converts the input current into a light signal on the transmitter, and then the receiver detects the target object according to the intensity or presence of the received light. The common photoelectric switch smoke alarm in the security system is often used in the industry to count the number of movements of the robotic arm.
Photoelectric switch model:
The photoelectric switch is a kind of sensor, which converts the change of the intensity of light between the transmitting end and the receiving end into the change of current to achieve the purpose of detection. Since the output circuit and input circuit of the photoelectric switch are electrically isolated (ie, electrically insulated), it can be used in many occasions. A new generation of photoelectric switch devices manufactured using integrated circuit technology and SMT surface mounting technology has intelligent functions such as delay, widening, external synchronization, anti-interference, high reliability, stable working area and self-diagnosis. This novel photoelectric switch is an active photoelectric detection system electronic switch that adopts pulse modulation. The cold light sources it uses include infrared light, red light, green light and blue light, etc., which can be non-contact and rapid without damage. And control the state and action of various solids, liquids, transparent bodies, black bodies, soft bodies and smoke. It has the advantages of small size, multiple functions, long life, high accuracy, fast response speed, long detection distance and strong resistance to optical, electrical, and magnetic interference.
Photoelectric switch manufacturers:
Use optical elements to change the light beam in the middle of the propagation medium; use the light beam to reflect the object; make the light beam return instantly after a long distance. The photoelectric switch is composed of three parts: transmitter, receiver and detection circuit. The transmitter is aimed at the target to emit a beam, and the emitted beam generally comes from a light emitting diode (LED) and a laser diode. The beam is emitted continuously, or the pulse width is changed. The radiation intensity of the pulsed beam has been selected many times in the launch, and it runs towards the target without indirectly. The receiver is composed of a photodiode or phototransistor. In front of the receiver, optical components such as lens and aperture are installed. Behind it is the detection circuit, which can filter out the effective signal and apply the signal.
Working principle of photoelectric switch:
After the modulated pulse generated by the oscillation circuit passes through the reflection circuit, the light pulse is radiated from the light emitting tube GL. When the measured object enters the range of the light receiver, the reflected light pulse enters the photosensitive transistor DU. The photoelectric switch demodulates the optical pulse into an electric pulse signal in the receiving circuit, and then is amplified by the amplifier and synchronized gating and shaping, and then the interference is eliminated by digital integration or RC integration, and finally the driver is triggered by a delay (or no delay) Output photoelectric switch control signal. Photoelectric switches generally have good hysteresis characteristics, so even if the detected object shakes in a small range, it will not affect the output state of the driver, so that it can be kept in a stable working area. At the same time, the self-diagnostic system can also display the light receiving status and stable working area to monitor the work of the photoelectric switch at any time.
Types of photoelectric switches:
The amplifier separation type is to separate the amplifier and the sensor, and is made with a dedicated integrated circuit and a mixed installation process. Because the sensor has the characteristics of ultra-small and multi-variety, the amplifier has more functions. Therefore, this type adopts the terminal block connection method and can be used for both AC and DC power supplies. With on and off delay function, you can set the light and sound switch, can control 6 kinds of output states, and have two output modes of contact and level.
The built-in type of amplifier integrates the amplifier and the sensor. It is made by ASIC and surface mounting technology, and it works with DC power supply. Its response speed situation (there are two kinds of 0.1ms and 1ms), can detect small and high-speed moving objects. Changing the polarity of the power supply can switch between bright and dark movement, and can set a self-diagnostic stable work area indicator. Both voltage and current output modes can prevent mutual interference, which is very convenient in system installation.
The built-in power supply unit integrates the amplifier, sensor and power supply device, and is made with a dedicated integrated circuit and surface mount technology. It generally uses AC power and is suitable for replacing contact type limit switches at the production site, and can be directly used for strong current control circuits. You can also set self-diagnostic stable working area indicator lights by yourself. The output is equipped with SSR solid state relay or relay normally open and normally closed contacts, which can prevent mutual interference and can be installed tightly in the system.
Photoelectric switch price:
Strong light source: The photoelectric switch can generally work stably when the ambient illuminance is high. However, it should be avoided that the optical axis of the sensor faces strong light sources such as sunlight and incandescent lamps. When the angle between the optical axis of the sensor (receiver) and the strong light source cannot be changed, a light-shielding plate or a long light-shielding tube can be installed around the sensor.
Mutual interference: MGK series of new photoelectric switches usually have the function of automatically preventing mutual interference, so there is no need to worry about mutual interference. However, when several groups of HGK series through-beam infrared photoelectric switches are installed in parallel and close to each other, the adjacent groups and mutual interference should be prevented. The most effective way to prevent this kind of interference is to set the emitter and the receiver crosswise, and open the group distance when more than 2 groups. Different frequency models can also be used.
The effective way of HGK series reflective photoelectric switch to prevent mutual interference is to open the interval. And the farther the detection distance is, the larger the interval should be, and the specific interval should be determined according to the debugging situation. Of course, models with different operating frequencies can also be used.
Photoelectric switch wiring diagram:
The slot photoelectric switch is usually a standard U-shaped structure. The transmitter and receiver are located on both sides of the U-shaped groove and form an optical axis. When the detected object passes through the U-shaped groove and blocks the optical axis, the photoelectric switch The detected switch signal is generated. The slot photoelectric switch is safer and more suitable for detecting high-speed changes and distinguishing transparent and semi-transparent objects.
Optical fiber photoelectric switches use plastic or glass optical fiber sensors to guide light, so as to realize the detection of objects not in the vicinity. Generally, fiber optic sensors are divided into through-beam type and diffuse reflection type.
related suggestion:
Photoelectric switch
Pepperl+Fuchs
liquid level sensor
Ultrasonic sensor
Surge protector
Safety barrier
Photoelectric switch article:
More than 150 years ago, communication pioneers boldly tried and costly to establish a telegraph line between North America and Europe. In the process, an astonishing number of cables were laid thousands of kilometers under the sea. Despite many challenges, they succeeded in establishing a connection, but only a few weeks later, it was damaged, partly because of cable limitations. Like these pioneers, Pepperl+Fuchs produces cables each year with lengths of thousands of kilometers, and these cables can meet almost all challenges. Today, let us learn more about Pepperl+Fuchs' 20 years of connection experience and the various applications of Pepperl+Fuchs sensor cables.
Reliable connection, originality
Whether it is machine building, welding, logistics, construction machinery or process industry, “powerful sensor technology requires powerful and reliable connection technology”, explained Mr. Jürgen Chrobak, managing director of Pepperl+Fuchs Group Hungary. In fact, seemingly simple sensor accessories are also an important part of automation technology. The failure of just one connector may cause the entire plant to fail and shut down, which will cost a huge price. "Saving the cost of connecting parts often leads to increased maintenance costs," said Mr. Roland Gubbels, Business Manager of Pepperl+Fuchs Connecting Parts.
In order to protect users from these risks, in Veszprém, Hungary, more than 200 Pepperl+Fuchs employees have developed, tested and produced high-quality automated cable assemblies for 20 years. What needs to be considered when developing connection technology? "As in many other fields, there are some challenges here. On the one hand, cables and connectors are highly standardized, which means that they are compatible with sensors regardless of the manufacturer. At the same time, Pepperl+Fuchs hopes to provide more than just standardization. Products," Mr. Gubbels said. To achieve this goal, Pepperl+Fuchs attaches great importance to more details, such as vibration protection, knurled nuts designed for safe installation, innovative snap-on design for protecting the cable layer, and 360-degree shielding.
"We have a clear understanding of customer needs-which cable should be used for which application. Our years of experience enable us to provide targeted, industry-specific solutions," Mr. Chrobak said.
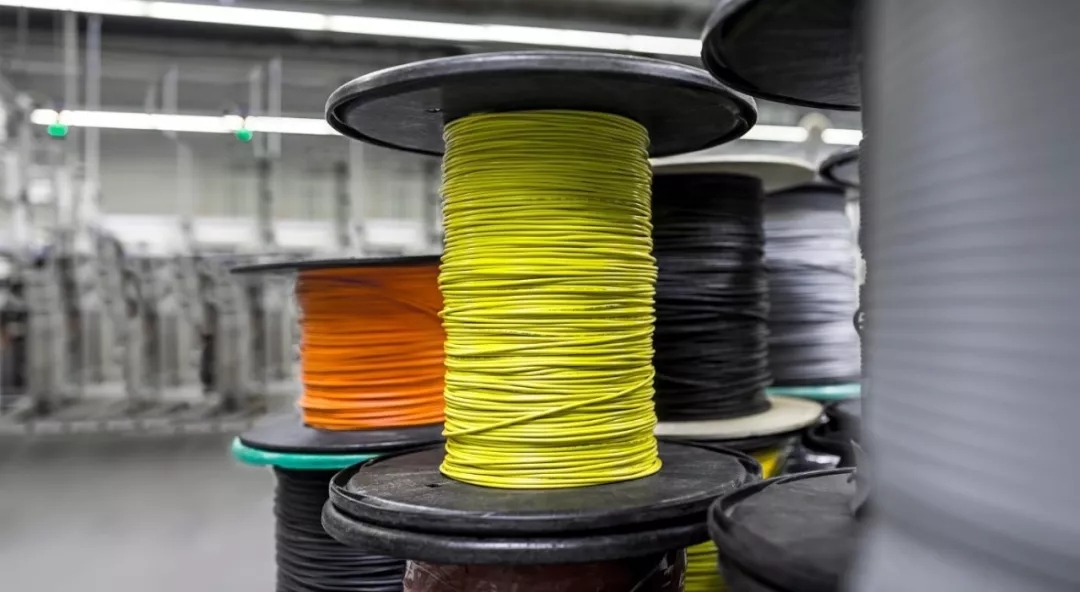
Food industry: cleaner and sanitary
In the food industry, safety and hygiene are the top priority. In any case, products and packaging will not be contaminated by contact with machine parts. The connector design plays a vital role: the surface must be smooth, easy to clean, and conform to the guidelines of EHEDG (European Hygienic Engineering and Design Organization). The accessories are made of stainless steel to ensure that no food sticks to the surface. High-quality connections must also be able to withstand intensive cleaning procedures and chemical reagents. "This is why Pepperl+Fuchs's 4-pin and 5-pin M8 and M12 connectors can meet the strict requirements of spraying and contact areas. They are also PVC and halogen-free, comply with FDA standards, and are certified ECOLAB. This combination ensures Cleanliness, and can be completely hygienic and safe during the cleaning of the machine and components," said Mr. Gubbels.
Robot industry: durable and highly flexible
Unlike food production, certain industries involve hazardous work. For these tasks, robots are used to perform millions of repetitive actions. In some areas, the robot movement may be extremely bending and rotating. To prevent production downtime, the connector must ensure constant power and data transmission between the robot and the automation system during use. "Pepper+Fuchs PUR-R cables can be twisted ±360° more than ten million times per meter. They ensure that every component in a highly automated production process can work reliably, withstand high temperatures, and is resistant to oil and chemical corrosion. PUR- R cables meet all these requirements because they are very flexible, suitable for drag chains, and can be twisted ten million times,” explains Mr. Gubbels.
For the automotive industry: resistant to welding slag splash
On the other hand, if cables are used in an environment with fumes and welding slag, they must be able to work reliably, even in the presence of huge direct or indirect heat. Fortunately, Pepperl+Fuchs has a long history as a supplier of automotive manufacturing and is very familiar with the stringent requirements of welding applications. PUR-A cables are designed for areas where the cable is in contact with welding spatter and requires a high degree of flexibility. However, in an extremely hot environment, such as a car body shop, the cable may come into contact with the spark stream, so special cables are required. "If the cable in your application is close to the welding process, you can choose POC coated cable. High mechanical strength, resistance to continuous working temperature up to 150 °C, resistance to welding spatter, these cables can be used for high temperature and welding where other cable types cannot work. Area where slag splashes," Mr. Gubbels said of this high-resistance special cable.
Special for construction machinery: more optimized design
Cables are not only exposed to extreme conditions in automobile manufacturing plants, but are also used in factory machinery and equipment. "With the launch of the professional MEC (mobile device connection) product portfolio, we are reducing the distance between the circular plug connector and the "auto world". Through our mature sealing design, we provide robust connectors for mobile devices. Gubbels Mr. said. It is based on the tried-and-tested connectors from Deutsch, AMP and TE Connectivity, which have been optimized by Pepperl+Fuchs for construction machinery applications. "Mobile device connector shells are overmolded to withstand harsh environments and provide long-lasting Protection, and can work in the temperature range of -50 to 105 °C. In addition, their slim design minimizes the space required for operation, and innovatively designed to protect the cable layer for reliable connection without the use of additional accessories," Gubbels added.