Pepperl+Fuchs inductive sensors are widely used in metal object detection
Pepperl+Fuchs inductive sensors are widely used in metal object detection
Pepperl+Fuchs inductive sensors are widely used in metal object detection
Keywords: photoelectric switch photoelectric switch manufacturer photoelectric switch model photoelectric switch price photoelectric switch wiring diagram photoelectric switch principle photoelectric switch type photoelectric switch application
Photoelectric switch:
The photoelectric switch is the abbreviation of the photoelectric proximity switch. It utilizes the shielding or reflection of the light beam by the detected object, and the circuit is connected by the synchronization loop to detect the presence or absence of the object. Objects are not limited to metal, all objects that can reflect light (or block light) can be detected. The photoelectric switch converts the input current into a light signal on the transmitter, and then the receiver detects the target object according to the intensity or presence of the received light. The common photoelectric switch smoke alarm in the security system is often used in the industry to count the number of movements of the robotic arm.
Photoelectric switch model:
The photoelectric switch is a kind of sensor, which converts the change of the intensity of light between the transmitting end and the receiving end into the change of current to achieve the purpose of detection. Since the output circuit and input circuit of the photoelectric switch are electrically isolated (ie, electrically insulated), it can be used in many occasions. A new generation of photoelectric switch devices manufactured using integrated circuit technology and SMT surface mounting technology has intelligent functions such as delay, widening, external synchronization, anti-interference, high reliability, stable working area and self-diagnosis. This novel photoelectric switch is an active photoelectric detection system electronic switch that adopts pulse modulation. The cold light sources it uses include infrared light, red light, green light and blue light, etc., which can be non-contact and rapid without damage. And control the state and action of various solids, liquids, transparent bodies, black bodies, soft bodies and smoke. It has the advantages of small size, multiple functions, long life, high accuracy, fast response speed, long detection distance and strong resistance to optical, electrical, and magnetic interference.
Photoelectric switch manufacturers:
Use optical elements to change the light beam in the middle of the propagation medium; use the light beam to reflect the object; make the light beam return instantly after a long distance. The photoelectric switch is composed of three parts: transmitter, receiver and detection circuit. The transmitter is aimed at the target to emit a beam, and the emitted beam generally comes from a light emitting diode (LED) and a laser diode. The beam is emitted continuously, or the pulse width is changed. The radiation intensity of the pulsed beam has been selected many times in the launch, and it runs towards the target without indirectly. The receiver is composed of a photodiode or phototransistor. In front of the receiver, optical components such as lens and aperture are installed. Behind it is the detection circuit, which can filter out the effective signal and apply the signal.
Working principle of photoelectric switch:
After the modulated pulse generated by the oscillation circuit passes through the reflection circuit, the light pulse is radiated from the light emitting tube GL. When the measured object enters the range of the light receiver, the reflected light pulse enters the photosensitive transistor DU. The photoelectric switch demodulates the optical pulse into an electric pulse signal in the receiving circuit, and then is amplified by the amplifier and synchronized gating and shaping, and then the interference is eliminated by digital integration or RC integration, and finally the driver is triggered by a delay (or no delay) Output photoelectric switch control signal. Photoelectric switches generally have good hysteresis characteristics, so even if the detected object shakes in a small range, it will not affect the output state of the driver, so that it can be kept in a stable working area. At the same time, the self-diagnostic system can also display the light receiving status and stable working area to monitor the work of the photoelectric switch at any time.
Types of photoelectric switches:
The amplifier separation type is to separate the amplifier and the sensor, and is made with a dedicated integrated circuit and a mixed installation process. Because the sensor has the characteristics of ultra-small and multi-variety, the amplifier has more functions. Therefore, this type adopts the terminal block connection method and can be used for both AC and DC power supplies. With on and off delay function, you can set the light and sound switch, can control 6 kinds of output states, and have two output modes of contact and level.
The built-in type of amplifier integrates the amplifier and the sensor. It is made by ASIC and surface mounting technology, and it works with DC power supply. Its response speed situation (there are two kinds of 0.1ms and 1ms), can detect small and high-speed moving objects. Changing the polarity of the power supply can switch between bright and dark movement, and can set a self-diagnostic stable work area indicator. Both voltage and current output modes can prevent mutual interference, which is very convenient in system installation.
The built-in power supply unit integrates the amplifier, sensor and power supply device, and is made with a dedicated integrated circuit and surface mount technology. It generally uses AC power and is suitable for replacing contact type limit switches at the production site, and can be directly used for strong current control circuits. You can also set self-diagnostic stable working area indicator lights by yourself. The output is equipped with SSR solid state relay or relay normally open and normally closed contacts, which can prevent mutual interference and can be installed tightly in the system.
Photoelectric switch price:
Strong light source: The photoelectric switch can generally work stably when the ambient illuminance is high. However, it should be avoided that the optical axis of the sensor faces strong light sources such as sunlight and incandescent lamps. When the angle between the optical axis of the sensor (receiver) and the strong light source cannot be changed, a light-shielding plate or a long light-shielding tube can be installed around the sensor.
Mutual interference: MGK series of new photoelectric switches usually have the function of automatically preventing mutual interference, so there is no need to worry about mutual interference. However, when several groups of HGK series through-beam infrared photoelectric switches are installed in parallel and close to each other, the adjacent groups and mutual interference should be prevented. The most effective way to prevent this kind of interference is to set the emitter and the receiver crosswise, and open the group distance when more than 2 groups. Different frequency models can also be used.
The effective way of HGK series reflective photoelectric switch to prevent mutual interference is to open the interval. And the farther the detection distance is, the larger the interval should be, and the specific interval should be determined according to the debugging situation. Of course, models with different operating frequencies can also be used.
Photoelectric switch wiring diagram:
The slot photoelectric switch is usually a standard U-shaped structure. The transmitter and receiver are located on both sides of the U-shaped groove and form an optical axis. When the detected object passes through the U-shaped groove and blocks the optical axis, the photoelectric switch The detected switch signal is generated. The slot photoelectric switch is safer and more suitable for detecting high-speed changes and distinguishing transparent and semi-transparent objects.
Optical fiber photoelectric switches use plastic or glass optical fiber sensors to guide light, so as to realize the detection of objects not in the vicinity. Generally, fiber optic sensors are divided into through-beam type and diffuse reflection type.
related suggestion:
Photoelectric switch
Pepperl+Fuchs
liquid level sensor
Ultrasonic sensor
Surge protector
Safety barrier
Photoelectric switch article:
Pepperl+Fuchs inductive sensor is a product of Pepperl+Fuchs, Germany. Pepperl+Fuchs is the inventor of sensing technology.
Pepperl+Fuchs factory automation branch, with rich products, including P+F safety barrier active isolators and passive isolators, Zener safety barriers and isolated safety barriers; industrial sensors include: capacitive sensors, inductive sensors, and tilt sensors , Ultrasonic sensors, photoelectric sensors, vision sensors, positioning systems, barcodes, two-dimensional barcode Data Matrix, AS-Interface, radio frequency identification RFID, connectors, rotary encoders, logic control units, and turnkey based on image processing and laser measurement technology Solution, the above products are mainly used in machinery and manufacturing. The following is a brief introduction to the Pepperl+Fuchs inductive sensor as an example
The working principle of Pepperl+Fuchs inductive sensors:
Pepperl+Fuchs inductive sensors are specially designed to detect metal objects. Its essence is composed of an oscillator, the detection surface is composed of a coil, and an alternating magnetic field is generated around the coil.
When a metal object is in the magnetic field generated by the Pepperl+Fuchs inductive sensor, the induced current will form an additional magnetic field to prevent the coil's magnetic field from alternating, and the oscillation will stop at this moment. This produces a normally open or normally closed output signal.
Advantages of Pepperl+Fuchs inductive sensors:
1. High work efficiency and quick response.
2. Strong resistance to industrial environment (sturdy products are completely encapsulated in resin).
3. There is no need to directly touch the detected object, so it can not only detect fragile and newly painted objects, but also avoid wear.
Application range of Pepperl+Fuchs inductive sensors:
Pepperl+Fuchs inductive sensors have a wide range of applications. They can detect without touching metal objects.
Mainly include: 1. Monitoring the movement of metal objects, counting, and so on. 2. Monitoring of machine parts (cam, stop, etc.)
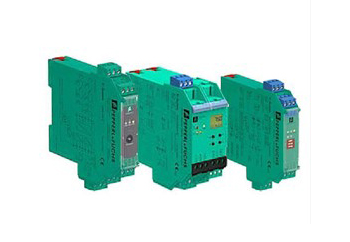
Not easy, extremely challenging
Before the "behemoth" made of steel weighing hundreds of metric tons can fly into the sky, it must be manufactured with the most advanced engineering technology and the highest precision, and must meet a variety of conditions to form the aerodynamic power required for aircraft flight. Therefore, the design must be accurate to ensure that the condition of the aircraft is nearly perfect. For example, external cracks and dents can have a catastrophic impact on the aerodynamics of the aircraft, and these potential hazards should be avoided at all costs.
The huge shape of the aircraft presents special challenges. Individual parts such as wings are several meters long, and the fuselage is longer, not to mention the huge engine. This makes the assembly of every aircraft component a very challenging task and requires millimeter-level accuracy. These advanced technologies can scan the overall height, width and length of large parts, providing important support for aircraft manufacturers and maintenance personnel in the correct assembly, quality control and regular inspections.
Piercing eyes, nuanced
Pepperl+Fuchs provides solid technical support for this challenge: the combined use of multiple 2D LiDAR scanner sensors can accurately detect and assemble large aircraft and their components. The calibrated sensors are located in different positions and can record target data from different angles. Combine all the data from the 2-D LiDAR scanner to form a three-dimensional point cloud to create an accurate digital image. The staff can use this image to accurately identify the structure and positioning of the components. Especially when the machine and parts need to be accurately positioned to avoid collisions when assembling various components.
Before the various parts of the aircraft are combined to form a whole, a system composed of multiple 2-D scanners escorts them. After all, it’s not uncommon for aircraft components to be produced in different locations: for example, a German-made fuselage, a French or American-made wing. In order to ensure that the components can be assembled together during the final assembly, the scanned data and the generated 3-D images can be compared with preset values and models at any time.
Cloud technology, connect the world
The data collected by multiple sensor systems can immediately provide the standard data format on the Pepperl+Fuchs subsidiary NeoNeon Cloud, which means that the three-dimensional images of the aircraft or its various components can be used anywhere in the world, also in the context of distributed production facilities. Now it's not just wing manufacturers who can compare their designs with manuscripts. Manufacturers located in other component production areas can also access the scanned data, and can use the 3D data for further processing to optimize the components, and even form the basis for their own production.
Copy success, improve efficiency
Those successful experiences in aircraft manufacturing can also be used for reference in many other application fields. Pepperl+Fuchs integrates multiple smart sensors to form a scanning technology that can not only capture large components and the overall space, but also accurately scan and capture small targets, larger targets, machines and even people. The 3D cloud of accumulated data points can be processed immediately by NeoNeon Cloud. They can be used all over the world, directly used in production, and even customized production of "one batch" can be achieved. This can flexibly meet and implement customer wishes and requirements, and enable companies with distributed production facilities to optimize plant utilization and increase efficiency.