The resolution and accuracy of the encoder2021
The resolution and accuracy of the encoder2021
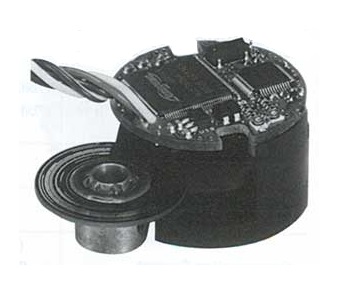
Regarding the understanding of the resolution and accuracy of the sensor, you can use the mechanical three-hand watch we use to make a metaphor: the resolution of the hour hand is hours, the resolution of the minute hand is minutes, the resolution of the second hand is seconds, and the eyes react quickly. , Through the space between the second hand in the second, we can even distinguish to about 0.3 seconds, which is what a three-handed mechanical pointer watch can do; and what is the accuracy is the accuracy of each watch to the standard time, which is Each watch is different, or it is different at different times of use (faster or slower as you go), roughly between 1 second and 30 seconds.
Similarly, in the use of rotary encoders, resolution and accuracy are two completely different concepts. The resolution of the encoder refers to the minimum angle change that the encoder can read and output. The corresponding parameters are: the number of lines per revolution (line), the number of pulses per revolution (PPR), the minimum step distance (Step), (Bit) etc. The accuracy of the encoder refers to the accuracy of the signal data output by the encoder to the measured real angle. The corresponding parameters are arc minutes (′) and arc seconds ("). Resolution: line, which is the encoder's The optical marking of the encoder disk, if the encoder is directly square wave output, it is the number of pulses per revolution (PPR) (Figure 1), but if it is a sin/cos signal output, it can be simulated by the signal The quantity change is electronically subdivided to obtain more square wave pulse PPR output (Figure 2). The square wave output of the encoder has phase A and phase B. The phase difference between phase A and B is 1/4 pulse period, through the rising edge and 1 /4 pulse period, by judging the rising edge and falling edge, you can get the change step of 1/4 pulse period (4 times the frequency), this is the minimum measurement step (Step), so strictly speaking, the minimum The measurement step is the resolution of the encoder.
For example, the 3600 line encoder of ROD426 from Heidenhain, Germany, the square wave output is 3600ppr, the pulse period is 0.1 degree, after passing the A-phase B-phase 4 times frequency, a measurement step of 0.025 degrees can be obtained; and the accuracy parameters it provides It is 18 arc seconds (0.005 degrees). If it is the 3600 line sine and cosine signal output of ROD486 from Heidenhain, it can be electronically subdivided by 25 times to obtain 90,000 pulses (ppr) and 0.004 degree pulse period. Through the quadruple frequency of A/B phase, it can be The resolution of the smallest measurement step of 0.001 degree is obtained, and the accuracy of the original encoder is 18 arc seconds (0.005 degrees, excluding the interpolation error). In the encoder or absolute encoder with communication data output, the output resolution is expressed in "bits", that is, the degree of division of the circle to the power of 2.
The accuracy of the rotary encoder, in the unit of arc minutes and arc seconds, has a little relationship with the resolution, but it is not all. For example, the ROD400 series of Heidenhain in Germany is still taken as an example. The line below 5000 lines is provided by Heidenhain. The accuracy is 1/20 of the width of the engraved line (related to the resolution), and for 6000-10000 lines, the accuracy is 12 arcseconds (independent of the resolution). And Heidenhain's RON series angle encoders are also 9000 lines-36000 lines. The accuracy of the RON200 series is 2.5-5 arcsec, the RON700 series is 2 arcsec, the RON800 series is 1 arcsec, and the RON900 series is 1 arcsec. It is 0.4 arcsec, which is not determined by the resolution. In fact, there are four parts that affect the accuracy of the encoder:
A: Optical part
B: Mechanical part
C: Electrical part
D: In the installation and transmission and reception parts in use, the accuracy after use is reduced, and the deviation of the mechanical part itself.
The influence of the optical part of the encoder on the accuracy:
Optical code disc-the main is the precision of the motherboard, the number of reticles per revolution, the precision of the reticle, the consistency of the width of the reticle, and the edge finish.
Light emission source-parallel and uniform light, light attenuation.
Light receiving unit-read the included angle, read the response.
The impact of the optical system after use-pollution, attenuation.
For example, optical code discs, first of all, the precision of the engraving of the mother board. HEIDENHAIN's mother board is recognized as the first in the world. It is said that it is processed in a double suspension workshop tens of meters underground, which reduces the influence of various external factors. Small to the smallest, even considering the infrasonic waves of the ocean waves and the vibration of the distant car engine, for this reason, many encoder manufacturers even buy templates from HEIDENHAIN. Secondly, the processing process, the time of optical imaging, temperature, physical and chemical changes, pollution, etc., will all affect the width and edge of the code disc marking line. Therefore, even with the same number of code disc markings, the accuracy that each company can achieve is different.
The influence of mechanical part of B encoder on accuracy:
The machining accuracy and installation accuracy of the shaft.
Bearing accuracy and structural accuracy.
The concentricity of the code disc installation, the accuracy of the optical component installation.
The concentricity of the installation positioning point and the shaft.
For example, in terms of the structure of the bearing, the bearing deviation of the single bearing support structure cannot be eliminated, and the deviation will be greater after use, while the double bearing structure or multiple support structure can effectively reduce the deviation of a single bearing. The influence of the electrical part of the C encoder on the accuracy:
The stability and accuracy of the power supply-the impact on the light emitting source and receiving unit.
Error caused by reading response and electrical processing circuit;
The influence of electrical noise depends on the anti-interference ability of the encoder electrical system;
For example, if electronic subdivision will bring errors, according to the introduction provided by Heidenhain, the electrical error of the subdivision of HEIDENHAIN encoders and the error of the sine-cosine curve are about 1% of the original reticle width. The accuracy impact brought by the use of D encoder:
The concentricity of the connection with the measuring shaft during installation;
The anti-interference and signal delay of the output cable (under longer distance or faster frequency);
Possible errors between the response of the receiving device and the internal processing of the receiving device.
The dynamic response deviation of the encoder during high-speed rotation.
The most common is the deviation between our own installation method and the installation result.
The impact of subdivision technology on resolution and accuracy
Interpolation and Digitizing Electronics
The voltage or current type sine-cosine wave signal is divided and converted into a square wave signal, which can be used for sensors with general sine-cosine wave signal output
The subdivision circuit determines the phase angle for the change in the waveform of the A/B phase, and then divides it into a finer square wave pulse output. It also provides 1/4 cycle A'/B' two-phase and Z'-phase, A' /B' phase can continue 4 times the frequency.
In fact, for the encoder after subdivision, the number of reticles before subdivision is very important, and the system accuracy before subdivision is even more important. Subdivision can adjust the high resolution, but it cannot improve the accuracy, or even reduce it. The accuracy.
So why do we sometimes feel that after subdivision, the processing accuracy is improved?
There are several factors here:
1. Before subdivision, the accuracy is far better than the resolution. After subdivision, the accuracy can be used more fully. For example, the ROD486 introduced above, 3600 reticles before subdivision, the resolution (Step), the step distance is 0.025 degrees, according to ±1 From the step distance, the accuracy is only 0.05 degrees, and the accuracy is 18 arc seconds. After subdivision, before 18 arc seconds, it can be used to improve the accuracy, but if the subdivision multiple is higher, the accuracy will be Unable to exceed 18 arc seconds.
2. At present, most of the motion control is controlled by the speed loop. The subdivision increases the resolution and can improve the accuracy of the speed loop. The final processing effect seems to be improved.
A high-resolution encoder does not necessarily have high accuracy. Take a Japanese 17-bit encoder as an example. Its original maximum engraved line is 8-bit 256 lines (as shown in Figure 3). After multiple subdivision and A/B phase 4 After frequency multiplication, a resolution of 17 bits (about 130,000 circular divisions) is obtained, and the converted angle resolution is 9.89 arc seconds. However, it does not provide accuracy parameters. For example, it is calculated by the method provided by Heidenhain with higher accuracy in the industry. The original accuracy (error) of the encoder system is 1/20 of the scaled line (512), and the interpolation error is 1% of the original scaled line (512). The obtained accuracy is 152 arcsec-equivalent to 2.5 arc minutes, so The accuracy proves that such a high-resolution variable rate encoder is mainly used in the speed loop, and the accuracy of the positioning position loop is not high. In fact, for the encoder after subdivision, the number of reticles before subdivision is very important, and the system accuracy before subdivision is even more important. Subdivision can improve the resolution, but it cannot improve the accuracy, and may even reduce it. Accuracy.
To sum up, there are many factors that affect the accuracy of the encoder. The accuracy of the encoder is related to the resolution, only the number of reticles in the optical part. The more reticles (the denser) the number, the higher the accuracy may be, but Look at many other parts, it has nothing to do with resolution. The number of reticle density is also limited by materials, processing technology and optical diffraction. Generally, the number of reticles of 58 mm outer diameter industrial encoders is up to 10,000 lines, and higher resolutions are subdivided by sine and cosine signals. When it is completed, its accuracy is also subject to certain restrictions.