What are the requirements for installation, maintenance and working environment of the coupling
What are the requirements for installation, maintenance and working environment of the coupling
What are the requirements for installation, maintenance and working environment of the coupling
What are the requirements for installation, maintenance and working environment of the coupling?
Coupling is the most commonly used connecting component in the shaft transmission of mechanical products; it connects two shafts to rotate together to transmit torque and motion, compensate the relative displacement of the connected two shafts and improve the transmission dynamics of the system. Its scope of application involves many areas of the national economy, and it is a universal basic component with many varieties and large usage. With the advancement of science and technology and the development of production, the types of mechanical products are increasing day by day, and the requirements for their use performance are also increasing. In order to meet the needs of various working conditions, couplings with various characteristics are required, and the expected use effect has been obtained.
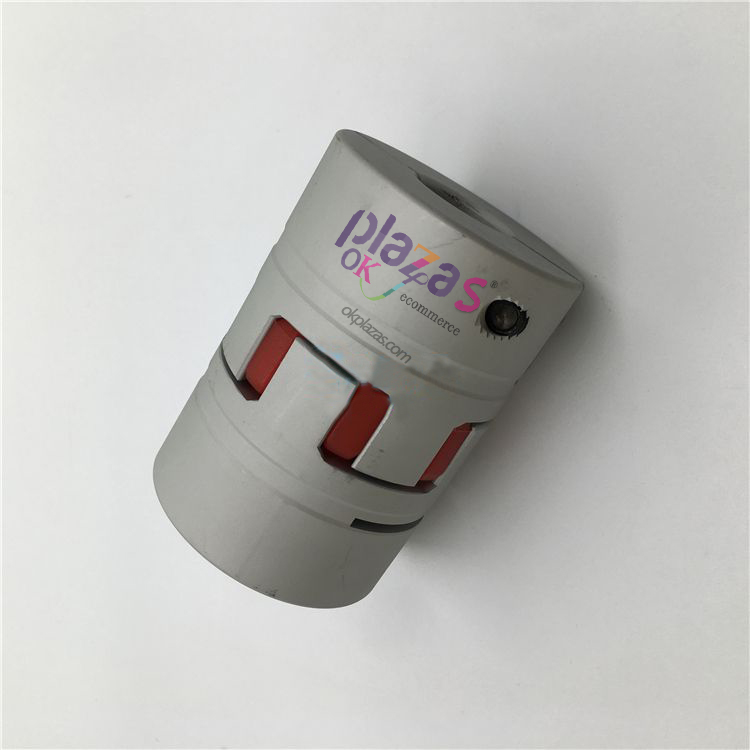
What are the requirements for installation, maintenance and working environment of the coupling?
The working environment must be considered when selecting the coupling and its protection measures, such as temperature, humidity, water, steam, dust, acid and alkali, oil, corrosive media and radiation. In the environment of high and low temperature, acid-base and corrosive media, metal elastic elements or flexible couplings with nylon or polyurethane as elastic element materials should be used, and flexible couplings with ordinary rubber as elastic element materials should not be used. The former has higher corrosion resistance, high and low temperature resistance, abrasion resistance and strength than rubber, but its elasticity and damping properties are not as good as rubber.
The types, forms, specifications and materials, manufacturing processes, precision and balance levels of couplings often vary greatly in manufacturing costs. When selecting the coupling, the appropriate coupling should be selected according to the specific work requirements and comprehensively considering the above factors.
What are the requirements for installation, maintenance and working environment of the coupling?
The use effect and life of the coupling is not only related to the performance of the product itself, but also closely related to its installation and adjustment. Proper installation and adjustment can make it fully effective and long-term safe operation, otherwise it will cause failure or even damage, and in serious cases, it will endanger the safety of the prime mover or working machine connected to it.
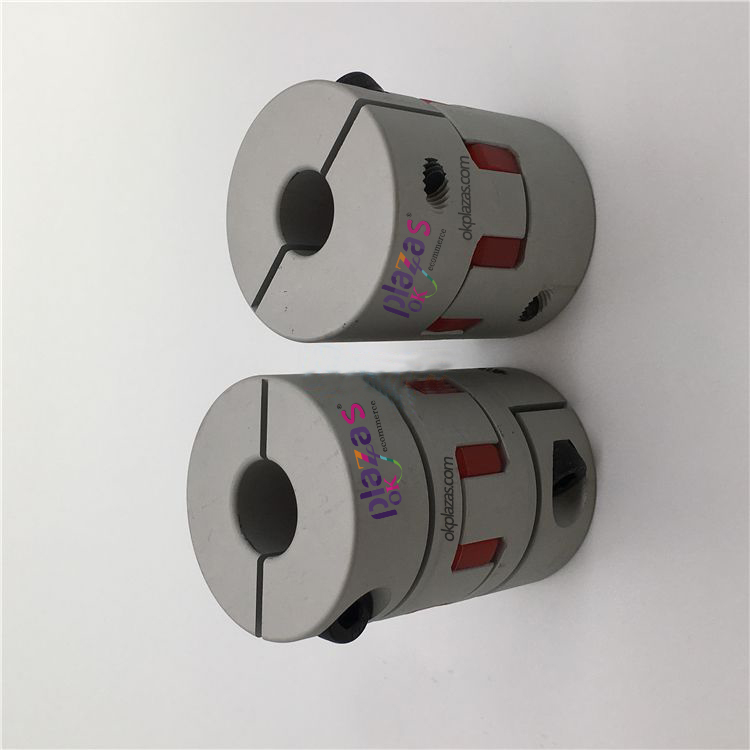
What are the requirements for installation, maintenance and working environment of the coupling? The installation of the coupling generally includes the assembly of the hub on the shaft, the centering and adjustment of the two shafts, and the internal connection of itself, which will be introduced separately below.
1. Coupling static press-in method
This method uses clamps, jacks, manual or motorized presses according to the amount of press-in force required during assembly. The static press-in method is generally used for tapered shaft holes. Because the static press-in method is restricted by the pressure machine, it is difficult to apply a large force when the interference is large. At the same time, the uneven small peaks on the mating surface between the coupling and the shaft will be cut off during the pressing process, which will damage the mating surface. Therefore, it is only suitable for the assembling of shafts and hubs with small transfer load and key connection, and is not suitable for the occasion of interference connection. The pressing force P during pressing can be calculated by the following formula:
Where df, Lf—combined diameter and length, mm; μ—combined surface friction factor, see Table 2-1; δmax—maximum interference; Ea, Ei—respectively the elastic modulus of the contained part and the contained part, MPa, see Table 2-2; da, di—respectively the outer diameter and inner diameter of the contained part (solid shaft di=), mm; v—Poisson’s ratio, see Table 2-2:
What are the requirements for installation, maintenance and working environment of the coupling?
2. Coupling power press-in method
This method refers to the use of impact tools or machinery to complete the assembly process, and is generally used where the coupling and shaft fit is transitional or has little interference. At the assembly site, the method of hammering is usually used. The method is to put wooden blocks or other soft materials on the end surface of the wheel hub as a buffer, and rely on the impact force of the hand hammer to knock in the elastic diaphragm coupling. This method has the risk of local damage to couplings made of brittle materials such as cast iron, quenched steel, and cast alloys, and should not be used. This method will also damage the mating surface, so it is often used for low-speed and small coupling assembly.
What are the requirements for installation, maintenance and working environment of the coupling?
3. Coupling temperature difference assembly method
The temperature difference assembly method refers to the use of heating the hub to expand or cooling the shaft to contract during assembly, thereby forming a gap between the mating surfaces, and inserting the shaft into the hole to achieve assembly. Heating or cooling during assembly can be used alone, or both can be used at the same time. This method does not damage the mating surface, and the force applied during assembly is small, so it is suitable for important connections or assembly of large parts.
Various methods such as oil bath heating, steam heating, flame heating, furnace heating and induction heating can be used to heat the hub. Among them, the oil bath heating temperature generally does not exceed 200 ℃, and the steam heating temperature does not exceed 120 ℃, both of which are suitable for connections with small interference. Oxygen acetylene or propane can be used for flame heating, and the heating temperature does not exceed 350°C. This method is suitable for small and medium-sized connectors that require strict control of local heating and thermal expansion. The induction heating temperature can reach 400℃, which is mainly suitable for heating large and medium connecting parts with extra heavy and heavy interference fit.
The heating temperature and time of the workpiece should be controlled well during hot loading. After heating, the heat preservation time should be longer for 0.5~2h. When the size of the workpiece is large, the heat preservation time should be longer.
The heating temperature of the workpiece during hot loading can be calculated as follows:
Fully understand the basic knowledge of couplings
In the formula, α—the coefficient of linear expansion of the material, ℃-1, see Table 2-3; △1—fitting interference, mm; △2—the minimum gap during hot mounting, see Table 2-4; t0—ambient temperature , °C. After hot-installing, the parts should be cooled naturally, not rapid cooling. After cooling, the gap between the part and the positioning surface due to shrinkage shall not be greater than 0.3/1000mm of the mating length.
The cooling of the workpiece usually adopts liquid nitrogen, liquid oxygen cooling, and can also adopt dry ice and cryogenic box cooling. Among them, the lowest cooling temperature of liquid nitrogen can reach -195°C, and the lowest cooling temperature of liquid oxygen can reach -180°C, both of which are suitable for cooling connections with larger interference. The lowest cooling temperature of dry ice cooling can reach -78℃, which is suitable for cooling small parts and thin-walled parts with small interference.
The lowest cooling temperature of the low temperature box can reach -140℃, which is generally suitable for cooling workpieces with higher matching accuracy. The cooling temperature and time during cooling are also strictly controlled to ensure smooth assembly. When the size of the workpiece is large, the freezing time will be longer so that it can be fully cooled.
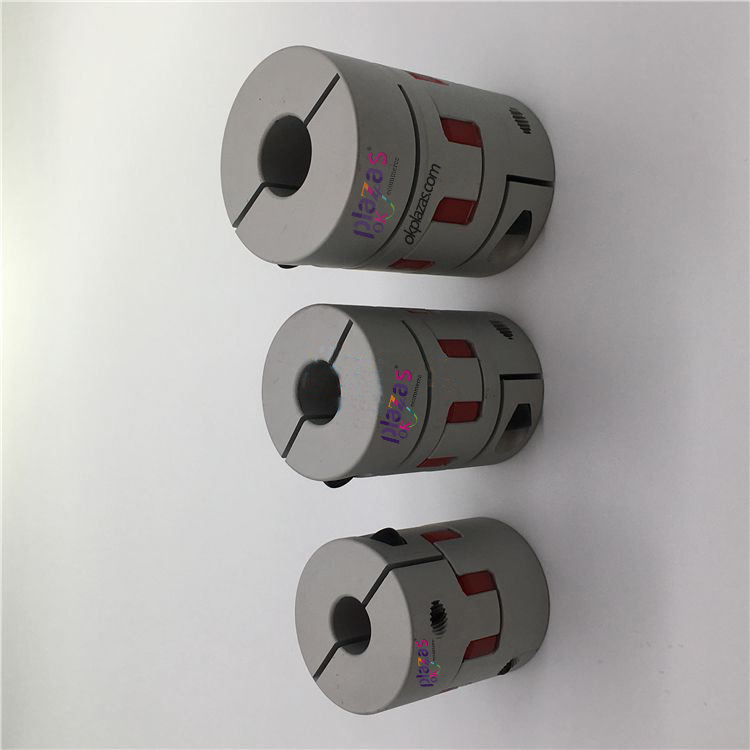
What are the requirements for installation, maintenance and working environment of the coupling?
4. Coupling hydraulic assembly method
For the assembly of large coupling hubs and shafts, hydraulic assembly is usually used. It uses a high-pressure oil pump and special tooling to send high-pressure oil between the hub and the surface of the shaft to expand the hub, and then gradually press the shaft and the hub together. During operation, pressurization and advancement can be performed alternately until all are loaded. Before assembling, pay attention to clean the mating surface and oil cavity with a clean white cloth and high-pressure oil, so as to avoid leaving impurities or dirt into the mating surface and affecting the assembly quality.
Hydraulic connection form
The cylindrical connection shown in (a) and (b) is the most commonly used connection form. It is generally assembled by temperature difference and disassembled by hydraulic pressure. When disassembling, high-pressure oil is used to guide the joint surface to make the travel gap between the containing part and the contained part, and then with the help of external force, the containing part is separated. Among them, the cylindrical connection with stepped shaft diameter shown in (b) has the dual functions of increasing the inner diameter of the containment member and pushing away from the axial direction when disassembling, so it has the self-unloading ability, so it is widely used.
(c), (d), where (c) has a sealing ring. Unlike cylindrical connections, conical connections can be assembled and disassembled using high-pressure oil.
(e) shows that the shaft and the inner hole of the intermediate sleeve are connected by a cylindrical surface, and the outer cone surface and the tapered hole of the intermediate sleeve are connected by a conical surface. This connection method can be repeatedly assembled and disassembled many times, and the middle sleeve is replaced as a vulnerable part. The assembly and disassembly method is the same as that of the general cone connection.
What are the requirements for installation, maintenance and working environment of the coupling?
5. Coupling expansion kit matching method
When the hub and the shaft are connected by an expansion sleeve, the joint surface should be cleaned first to ensure that there is no dirt, corrosion and damage, and at the same time, apply a layer of non-uniform coating evenly on the joint surface of the expansion sleeve and the connector. The thin lubricating oil containing molybdenum disulfide additives, after the hub is moved to the designated position on the shaft, the expansion sleeve of the loosened screw is smoothly inserted into the connecting hole, and the connecting piece is not skewed by hand. Tighten the screws. When tightening the expansion sleeve screws, use a torque wrench to tighten them diagonally, crosswise, and evenly at 1/3, 1/2, and 1 of the specified torque three times. Finally, check all the screws with the specified torque.