What are the structural characteristics and applications of the encoder
What are the structural characteristics and applications of the encoder
What are the structural characteristics and applications of the encoder
What are the structural characteristics and applications of the encoder?
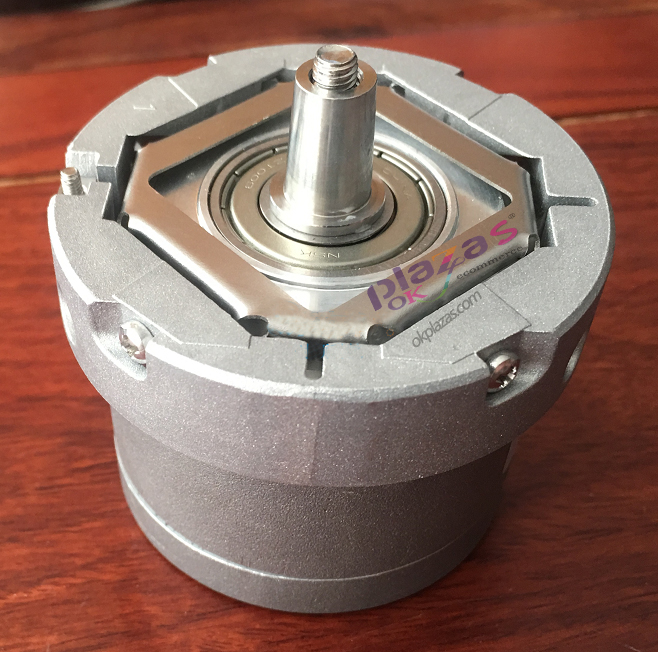
Encoder is a device that compiles and converts signals or data into signal forms that can be used for communication, transmission and storage. Indeed, the encoder is only a small part. But it may be used on machines that no one has even thought about. Now, we all know that the encoder is used in conjunction with the motor. There are millions of possibilities in the world, and the combination of an encoder and a motor (servo motor encoder) is only a drop in the ocean, and it has more applications that you would never expect.
Those who are familiar with motion control will know familiar encoders. But for those who have not touched the encoder, the encoder is relatively unfamiliar. Therefore, the editor of okplazas.com introduces the function of the encoder by taking the elevator in our daily life as an example. Before the introduction, let us imagine the process of riding an elevator. We pressed the "△▽" button, but after a while, the elevator would come to our floor, then the door would open automatically, and then we would enter the elevator. After entering the elevator, we press the button of the corresponding floor. The elevator door closed automatically, taking us to the corresponding floor, and the elevator door opened again.
In the motivation of this series of processes, two encoders actually play an important role. I wonder if you know? First, the first encoder controls the motor to move the elevator. Because the elevator relies on the motor to rotate up and down, as long as the direction of rotation is clear, it can be judged whether the elevator is up or down. In addition, the encoder can also detect the movement of the motor (number of rotations & 41;), so as to know exactly how much the elevator has moved. Using the information provided by these encoders through the elevator control panel, the elevator can quickly and stably reach the designated floor.
The other elevator door is automatically controlled by an encoder. We often look at the elevator switch. It is obvious that it has a subtle and precise control. The opening and closing time of the elevator doors is very precise. In the process of opening the elevator door, the running speed of the elevator door can be accelerated and the realization time can be shortened. Through the encoder, the movement and control of the motor can be correctly mastered, and the general soft motion of the silk fabric can be realized.
When elevators appear in people's field of vision, encoders are not popular. More than all the encoder work is done manually. At the beginning, there was no "△▽" button, and the bell was used. We can see this scene in the movies of the Republic of China. The Shanghai tycoon enters the elevator, and the attendant in the elevator rings the bell to get off the gate to make the elevator reach the corresponding floor. But now, due to the use of encoders to determine the rotation direction and number of rotations of the motor, elevators have become more and more convenient and no longer need to be manually operated as before.
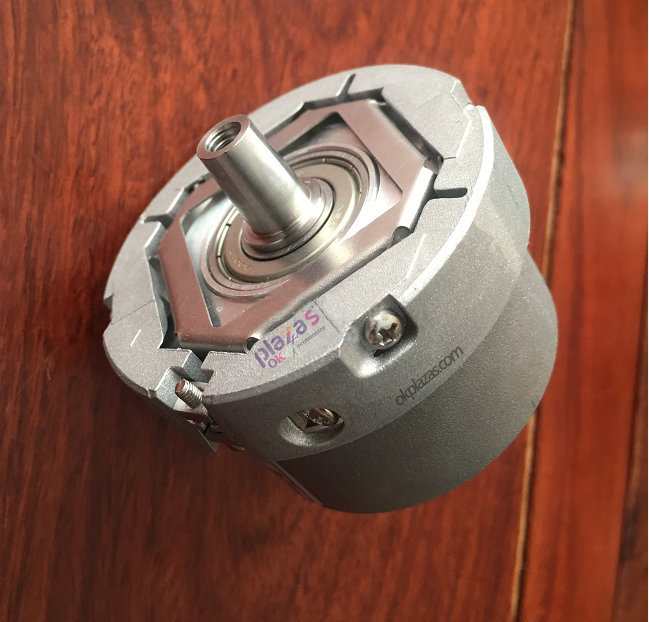
What are the structural features and applications of the encoder?
So how to use the encoder to know the "rotation direction", "rotation position" and "rotation speed"? This time, the optical transmission encoder is briefly introduced. The transparent encoder is mainly composed of four parts: ①LED light-emitting element; ②lens; ③code plate; ④light receiving IC.
First, the light of the LED luminous body is disordered light. The light is gathered together by the lens and converted into parallel light. Open multiple rectangular holes (with or without lights) evenly on the code board. It is emitted to the light-emitting diode and other electronic components on the light receiving IC, and processed by the signal conversion electronics. Finally, two square waves of phase A and phase B are output.
The phase relationship between A phase and B phase is universal in the world. The phase difference between phase a and phase B is 14 cycles of output. By processing the output signals of the A and B phase encoders, the rotation direction, position and speed of the motor can be clearly displayed. Then we will discuss how to detect them.
What are the structural features and applications of the encoder?
By detecting the sequence of phase a and phase B, the rotation direction of the encoder can be detected. For example, when the encoder rotates clockwise, phase a appears after phase B. If the encoder rotates counterclockwise, phase B will appear before phase a. This structure can not only determine the direction of rotation, but also determine the horizontal drive. The direction of movement.
Encoder rotation position detection
The code disc (grating disc) is a circular plate with a certain diameter evenly opened with a number of rectangular holes. There are 360 rectangular holes in our house a week. Because each rectangular hole outputs a pulse signal, it can be detected that each pulse has the same rotational position as one degree. If there are 3600 rectangular holes in a circle, an angle of 0.1 degree can be detected.
Detect the speed of the encoder
Measure the output pulse frequency and encoder resolution, and then easily calculate the encoder speed according to the following formula.
Rotation speed (Rmin) = (pulse frequency resolution) * 60
Flexible use of encoders can control the rotation direction, position and speed of the motor. In the above elevator example, as shown in Figure 4, the microprocessor sends out a control signal to drive the motor, and the encoder mounted on the motor shaft outputs the signal. Then use the encoder counter to process the output of the encoder and compare it with the control signal of the microprocessor. By comparing the control signal of the driving motor and the result of the motor rotation, only the power required by the target speed is provided to the motor. In this closed structure, we call it a closed loop.
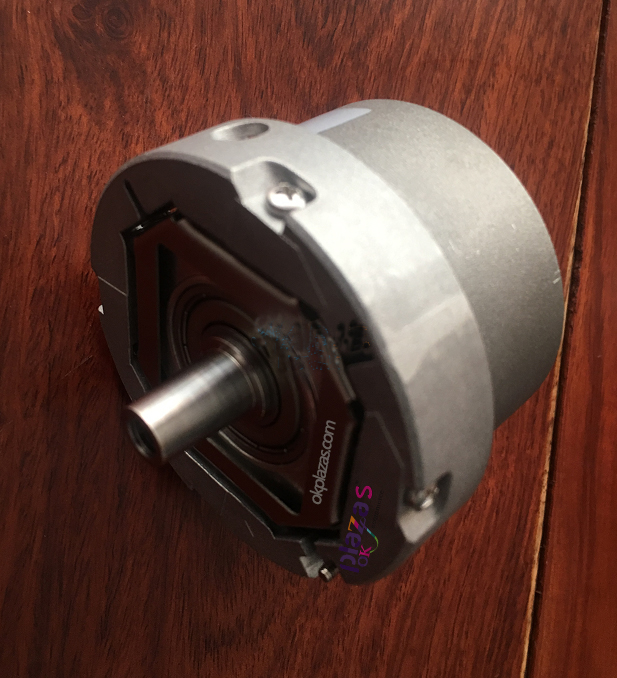
What are the structural features and applications of the encoder?
To achieve high-precision calculations
Having said that, we must have a general understanding of the operation of the encoder. Now let us return to other applications of the encoder.
If someone asks you what the encoder does? The simplest method is to measure the direction, number, and angle of rotating or moving objects. Therefore, generally speaking, the application of encoders can refer to motor-driven machines.
However, it seems that the scope is too wide. More precisely, it is high-precision mechanical equipment. For household appliances like electric fans, there is no problem with brushless motors, so no coding is required. On the contrary, in industrial equipment such as industrial robots, AGVs, and modules, encoders are widely used in these equipment due to the requirements for high-precision operation. In addition, the elevator introduced at the beginning of the article has very high requirements for its own motion and will also use an encoder. In recent years, encoders have become more and more widely used in hybrid vehicles and electric vehicles.
What are the structural characteristics and applications of the encoder?
Where there is a motor there is an encoder
Did you realize that all the encoder applications introduced so far are related to electricity? For rotating or horizontal movement, in addition to electric motor driving as a power source, oil pressure and air pressure are also used as driving methods. But these hydraulic and pneumatic devices basically do not use encoders. why? First of all, the motor can be started or stopped immediately by controlling the power switch. By controlling the motor voltage and frequency, the number of revolutions can be easily changed. Because these actions have a high response, the motor can be controlled with high precision and speed through the encoder.
If oil pressure is used as the power source, it takes time for the oil pressure to rise (such as a propeller), and it cannot be controlled by an encoder like a motor. It is not only when the propeller starts to move, but when the number of revolutions is to be changed, the propeller cannot respond immediately and can only change slowly. This is because the oil pressure driving the propeller is restricted by the viscosity of the oil and the resistance of the pipeline. The change of oil pressure and the lag of the propeller's revolutions make it extremely difficult to measure the revolutions with an encoder for control, the same is true for pneumatic equipment.
The above is about the okplazas.com high-precision encoder manufacturer: What are the structural characteristics and applications of the encoder? Welcome friends who are interested to exchange and study together.