What are the structural characteristics and installation applications of absolute encoders
What are the structural characteristics and installation applications of absolute encoders
What are the structural characteristics and installation applications of absolute encoders
What are the structural characteristics and installation applications of absolute encoders?
The encoder can convert the angular displacement or linear displacement into a digital quantity through simple conversion, so the corresponding encoders are divided into angle digital encoders and linear displacement encoders. Modern encoders have higher resolution, better reliability and higher accuracy than any pattern sensor of the same size today. The resolution of the code disc sensor made by the encoder depends on the number of code channels. Currently, encoders that provide 20-bit or 21-bit binary output have been produced.
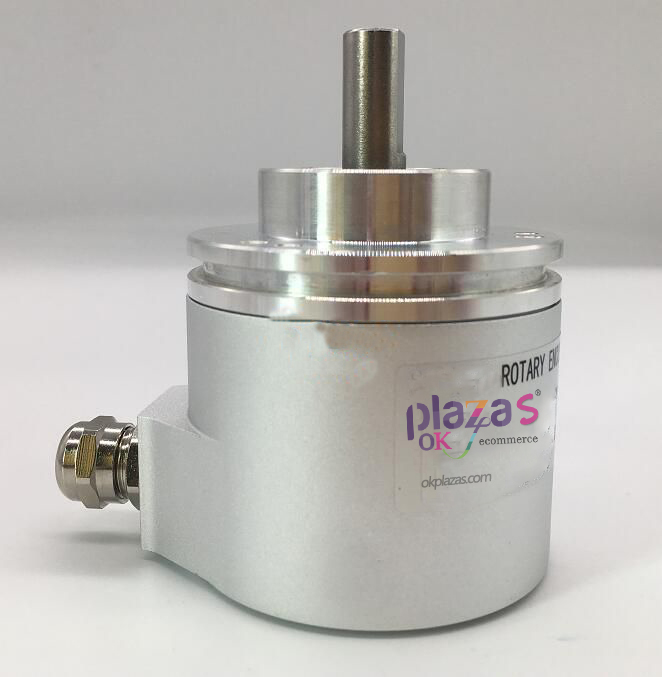
Absolute type rotary photoelectric encoder, because of its absolute unique position, anti-interference, no power-down memory, has been more and more widely used in angle, length measurement and positioning control in various industrial systems.
There are many lines on the CD of the absolute encoder. Each row is divided into 2 rows, 4 rows, 8 rows, and 16 rows. . . In this way, at each position of the encoder, by reading the open and dark of each marking, a set of unique binary codes (Gray codes) from the zero power of 2 to the N-1 power of 2 can be obtained, called It is an N-bit absolute encoder. This kind of encoder is determined by the mechanical position of the encoder, and is not affected by power failure and interference. The absolute encoder is the uniqueness of each position determined by the mechanical position. It does not need to be memorized, does not need to find a reference point, and does not need to be counted all the time. When the position needs to be known, when to read its position. In this way, the anti-interference performance of the encoder and the reliability of the data are greatly improved.
Because absolute encoders are significantly better than incremental encoders in positioning, they are increasingly used in industrial control positioning. Absolute encoders have high accuracy and large output bits. If parallel output is still used, the output signal of each bit must be well connected. For a more complex working environment, isolation must be carried out, and there are many connecting cable core wires, which brings a lot of inconvenience to work and reduces reliability. Therefore, among the multi-bit output types, absolute encoders generally use serial output or bus output, and SSI (synchronous serial output) made in Germany is the most commonly used serial output for absolute encoders.
The rotation of a single-turn absolute encoder is used to measure the lines of the disc during the rotation process to obtain a unique code. When the rotation exceeds 360 degrees, the code returns to the origin, which does not comply with the principle of absolute code uniqueness. This kind of encoder can only be used for measurement within a 360-degree rotation range, and is called a single-turn absolute encoder.
The encoder manufacturer uses the principle of the clock gear mechanism. When the center code disc rotates, another group of code discs (or multiple sets of gears, multiple sets of code discs) are driven by gears, and the number of revolutions is increased on the basis of single-period encoding to expand the measuring range of the encoder. This type of absolute encoder is called a multi-turn absolute encoder, and it is also unique for each position code determined by the mechanical position and does not need to be memorized.
Another advantage of the multi-turn encoder is that due to the large measurement range, the actual use is often abundant, so there is no need to find a change point during the installation process, and the lower position can be used as the starting point, which greatly simplifies the difficulty of installation and debugging. Multi-turn absolute encoders have obvious advantages in length positioning, and are increasingly used in industrial control positioning.
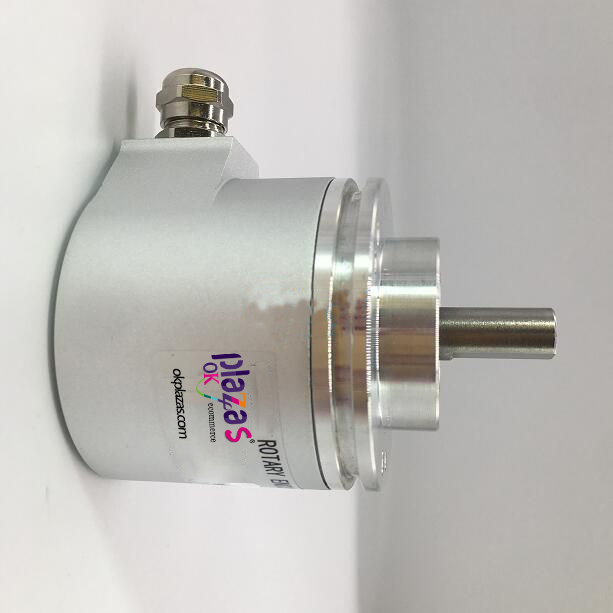
What should be paid attention to during the use and installation of absolute encoder?
The mechanical installation of absolute rotary encoder includes high-speed end installation, low-speed end installation, and auxiliary mechanical device installation.
High-speed end installation: installed on the shaft end of the motor (or gear connection). This method has the advantage of high resolution. Since there are 4096 multi-turn encoder cycles and motor revolutions within this range, the resolution can be improved by using the full range. The disadvantage is that there is a gear gap error when the moving object passes through the reduction gear, which is generally used for one-way high-precision control, such as roll gap control during rolling. In addition, the encoder is directly installed at the high-speed end, so the motor jitter must be small, otherwise the encoder will be easily damaged. Low-speed end installation: installed after the reducer, such as the shaft end of a winding rope drum or finally the shaft end of a reducer. This method does not require gear return, and the measurement is more direct and accurate. This method generally measures remote positioning, such as the positioning of various lifting equipment and feeding carts. Auxiliary machinery installation: commonly used gears and racks, chain belts, friction wheels, rope winding machinery, etc.