What are the structure and application scenarios of the encoder?
What are the structure and application scenarios of the encoder?
Encoder is a kind of sensor, which is mainly used to detect the movement speed, position, angle, distance or counting of machinery. In addition to industrial machinery, many motor control servo motors and BLDC servo motors also include motor controllers. According to the detection principle, the encoder can be divided into optical type, magnetic type, induction type, and electrostatic capacitance type. According to its scale method and signal output form, it can be divided into incremental encoder and absolute encoder. The photoelectric encoder uses the principle of grating diffraction to realize displacement-digital conversion. It has been applied to machine tools and computers since the 1950s. Because of its simple structure, high measurement accuracy, and long life, it has been valued and popularized at home and abroad, with precise positioning, speed, Length, processing.
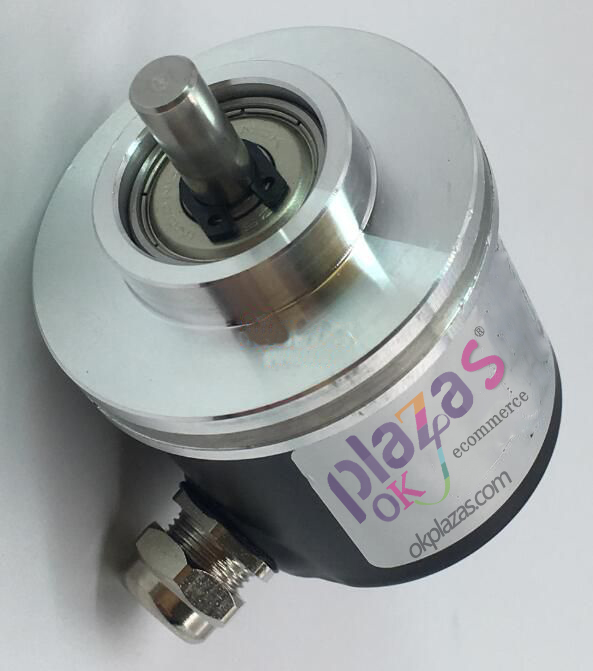
The encoder is a precision measuring device that combines mechanical and electronic closely. It is used to encode, convert, communicate, transmit and store signal data to signals and data. According to the characteristics, encoders are classified as follows.
Code disk and code ruler: The encoder that converts linear displacement into electrical signals is called code ruler, and the code disk that converts angular displacement into telecommunications.
Incremental encoder: Provides information such as position, angle, number of turns, and defines the resolution with the number of pulses per revolution.
Absolute encoder: Provides position, angle, number of turns and other information in angle increments, and assigns a unique code to each angle increment.
Hybrid absolute encoder: The hybrid absolute encoder outputs two sets of information. A group of information is used to detect the position of the magnetic pole and has an absolute information function. The other group has the same output information as the incremental encoder.
What are the structure and application scenarios of the encoder?
The difference between incremental and absolute encoders
The incremental encoder converts the displacement into a periodic electric signal, and converts the electric signal into a counting pulse again. The number of pulses represents the magnitude of the displacement. In the absolute encoder, each position corresponds to a specific digital code, which has nothing to do with the middle process of measurement, and only displays the values related to the start and end positions of the measurement.
What are the structural application scenarios of the encoder? Why should an encoder be installed in the motor? ?
When using an incremental encoder, the position is determined by the number of pulses calculated from the zero mark, but the position of an absolute encoder is determined by the read value of the output code. Within a week, the reading of the output code of each position is unique. Therefore, when the power is turned off, the absolute encoder will not be separated from the actual position. Even if the power is turned on again, the position reading value is still valid.
Parameters that should be decided when selecting an encoder
Installation size, wire method and protective device. There are 2 types of positioning stopper, shaft diameter, mounting hole position, and cable lead mode. Whether the protection level of the installation space volume and working environment meets the requirements.
Resolution. The number of pulses output per revolution when the encoder is operating.
Encoder output electrical interface. . The common ones are push-pull output type, voltage output, open collector, line driver output type. Its output mode must be consistent with the interface circuit of its control system.
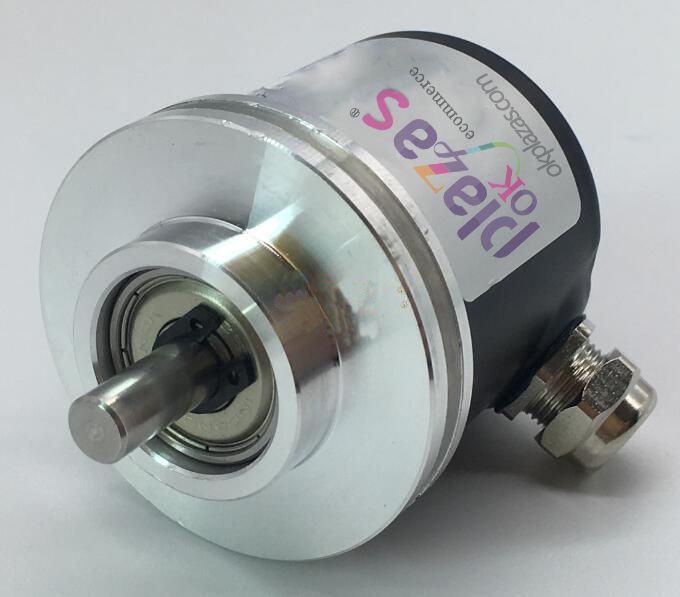
What are the structure and application scenarios of the encoder? Encoders commonly used in motors
Incremental encoder.
Directly use the photoelectric conversion principle to output 3 groups of square wave pulses a, b, and z phases. A, b two sets of pulse phase difference of 90o can easily determine the direction of rotation. Each z-phase rotates 1 pulse for the positioning of the reference point. Its advantages: simple structure, average mechanical life of more than tens of thousands of hours, strong anti-interference, high reliability, and suitable for long-distance transmission. Disadvantages: Cannot output absolute position information of shaft rotation.
Absolute encoder
Sensors that directly output digital quantities. The sensor circular code disc has several concentric code channels in the radial direction. Each channel is composed of a transparent sector area and an opaque sector area. The number of sectors of adjacent code channels is twice as large. On the other hand, when the code disk is located at different positions, each light receiving element transforms the corresponding level signal according to whether or not it receives light to form a binary number.
The feature of this encoder is that it can read the digital code corresponding to the position fixed at any position of the rotating shaft without a counter. Of course, the more code channels, the higher the resolution. For an encoder with n-bit binary resolution, the code disk needs n bar code channels. Now there are 16-bit absolute encoder products in China.