What are the working principles and characteristics of servo motor encoders?
What are the working principles and characteristics of servo motor encoders?
What are the working principles and characteristics of servo motor encoders?
What are the working principles and characteristics of servo motor encoders?
Encoders are generally divided into two types: incremental and absolute. The biggest difference is: in the case of an incremental encoder, its position is determined by the number of pulses calculated from the zero position, while the position of an absolute encoder Determined by the reading of the output code. In a circle, the output code reading of each position is unique; therefore, when the power is turned off, the absolute encoder will not be separated from the actual position. If you turn on the power again, the position reading is still valid; unlike an incremental encoder, the zero mark must be found.
Encoder manufacturers have a complete set of products, which are generally dedicated, such as elevator dedicated encoders, machine tool dedicated encoders, servo motor dedicated encoders, etc., and the encoders are intelligent and have various parallel interfaces to communicate with other equipment. Such as servo motor encoder.
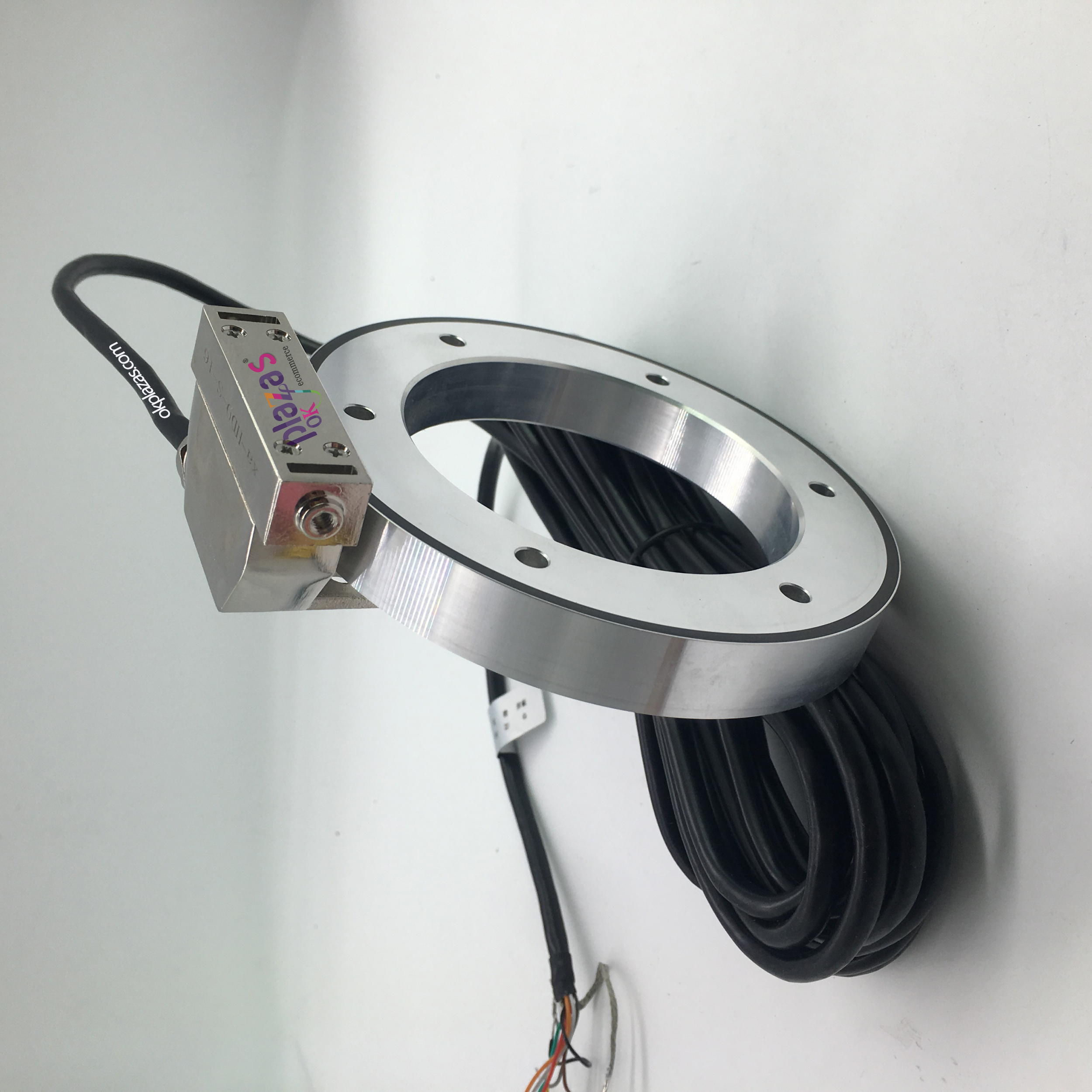
Servo motor encoders are actually similar in function to ordinary encoders, but they also have special features. Because they use synchronous motors, they use stronger signals, and their structure is more complex, requiring more professional personnel to operate.
The servo motor encoder has a 90 degree difference between the phases A and B. You can compare the phase A or the B phase to determine the forward and reverse rotation of the encoder. The zero position of the encoder can be obtained through the zero pulse. Reference bit.
The materials of the encoder code disc are glass, metal, plastic. The glass code disc is deposited on the glass with very thin scribe lines, which has good thermal stability and high precision. The metal code disc is directly engraved with through and impassable lines and is not fragile. However, due to the certain thickness of metal, the accuracy is limited, and its thermal stability is one order of magnitude worse than that of glass. Plastic code discs are economical, and their cost is low, but the accuracy, thermal stability, and use time are shorter.
Servo motor encoder resolution—The number of open or dark engraved lines provided by the encoder per 360 degree rotation is called resolution, also called resolution indexing, or the number of lines directly, generally 5 to 10,000 lines per revolution.
Servo motor encoder with high resolution, programmable encoder, dedicated to demanding applications
Compact installation size
Resolution up to 16 bits
Programmable: output voltage, zero pulse position, zero pulse width, number of pulses and counting direction
Optional connection method: axial or radial cable outlet, M23 or M12 connector (axial or radial).
Electrical interface: 5 V & 24 V TTL/RS-422, 24 V HTL/push-pull, 5 V Sin/Cos 1 Vss
Mechanical interface: clamping flange or servo flange, blind hollow shaft or through hollow shaft
The servo motor encoder can set the zero point remotely.