What is the significance of the absolute encoder emphasizing the concept of absolute
What is the significance of the absolute encoder emphasizing the concept of absolute
What is the significance of the absolute encoder emphasizing the concept of "absolute"?
What is the significance of the absolute encoder emphasizing the concept of "absolute"?
The encoder can provide feedback for movement in various applications, such as placing the patient in the appropriate position of the MRI machine or filling beverages at a rate of 300 bottles per minute. When selecting an encoder, the user must consider some critical application characteristics: Is it to track linear motion or rotary motion? Is it an optical encoder or a magnetic encoder? In addition, in order to successfully implement professional applications, users should also consider whether to choose an incremental encoder or an absolute encoder-even if the same sensing mechanism is used, the performance of the two encoders is quite different. To achieve a successful application system, you need to understand all the relevant characteristics of the above two encoders and make the right choice.
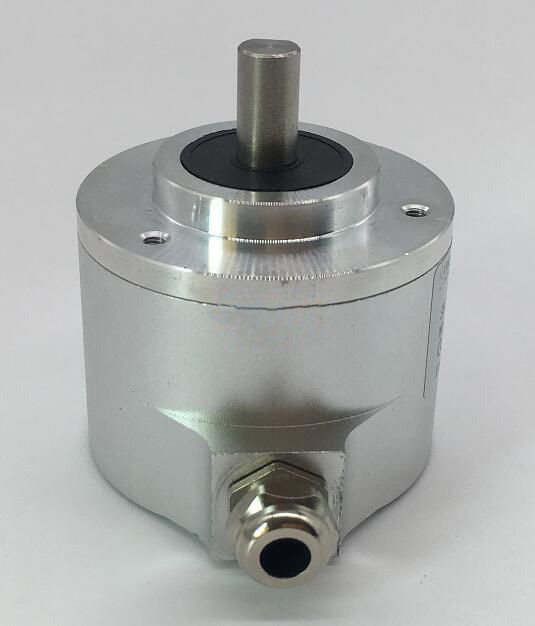
As the name suggests, an absolute encoder can record the position of the encoder in an absolute coordinate system, and an incremental encoder can output the incremental changes of the encoder from a predefined starting position. Incremental encoders require additional electronic equipment (usually PLCs, counters or inverters) to count pulses and convert pulse data into speed or motion data, while absolute encoders can generate numbers that can identify absolute positions signal. In summary, incremental encoders are usually more suitable for simple applications with low performance, while absolute encoders are the best choice for more complex critical applications-these applications have higher speed and position control requirements . The output type depends on the specific application.
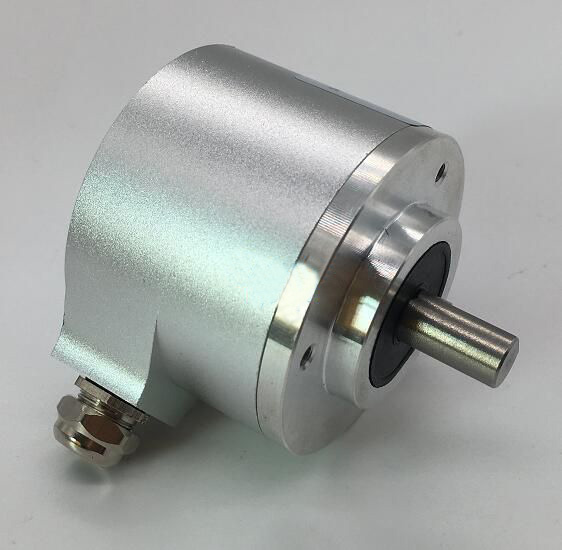
What is the significance of the absolute encoder emphasizing the concept of "absolute"?
1) An absolute code value can be provided for each axis position. Especially in position control, the absolute value encoder does not need to count, and can achieve direct internal high-speed reading and external output. This is the "high speed" and "economical" characteristics of the absolute value encoder, which can reduce subsequent receiving device control It also reduces the cost of other additional input components. For example, an industrial robot that works in parallel on multiple axes can realize high-speed multi-axis parallel and synchronous work. And various control fields that require multi-axis synchronization.
2) Absolute encoders without counting need no reference drive after the power is turned on or the internal and external power fails, and the current accurate position can be obtained after the power is normal. In the complex interference situations in various industrial electrical environments (such as the interference between the inverter and the motor), the original position information of the absolute encoder is absolute and will not be affected by the interference. The above-mentioned characteristics determine the safety and reliability of this encoder, and it can be used in occasions with safety requirements, such as wind power pitch system, port machinery synchronous positioning, lifting machinery, construction machinery (tower crane), elevators, engineering Machinery, iron and steel metallurgy, petrochemical industry, water conservancy and electric power, medical equipment radar artillery slewing device, solar tracking slewing device, etc., as well as large industrial robots in the fields of heavy industry, nuclear industry, and automobile manufacturing.
3) Today, fast and reliable digital data transmission is already one of the core elements of absolute encoders, industrial standard Canopen, Profibus-DP fieldbus, Profinet, Earthnet industrial Ethernet, Endat2.2, Hiperface, Biss, dedicated high-speed RS485 with CRC data security, and other high-speed data transmission protocols dedicated to servos and robots, the original incremental encoder that sends information in a "pulse" mode cannot be realized. This is the high-speed bus-type feature of the absolute encoder.
4)The high-digit resolution feature of the absolute value encoder, because it does not need internal and external counting and directly outputs digital signals, it is no longer confused by reading "pulse" and "accumulation" and the response speed can not keep up in high speed , The combination of advanced digital and analog technologies, absolute encoders have been able to achieve high-bit resolution, such as the 25-bit single-turn of the German absolute encoder (2 to the 25th power within 360 degrees). The resolution can be satisfied with the high-speed and precise positioning of the servo motor and the robot and the minimum step jitter. For example, accurate calculation of high-order position derivatives such as acceleration and jerk (kinematic rigidity), accurate positioning of the minimum shaking of the front end of the robot arm, etc.
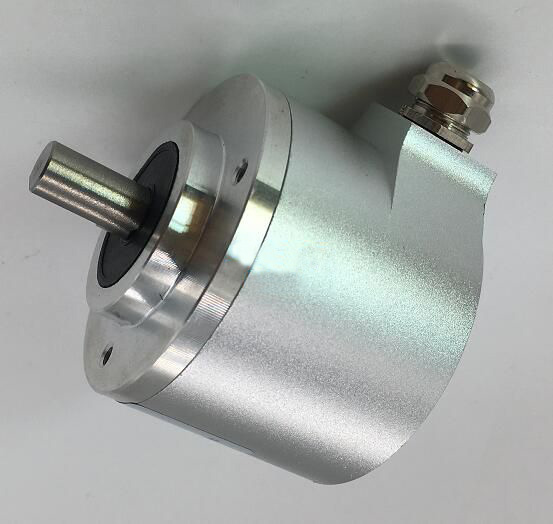
What is the significance of the absolute encoder emphasizing the concept of "absolute"?
Absolute encoders are suitable for applications where safety issues are critical and the encoder is not allowed to return to the initial position, such as high-performance CNC machine tool applications. In addition, this type of encoder is also an ideal choice for applications where returning to the initial position will greatly increase the operating time or application cost. For example, if the power supply of the DNA sequencer is interrupted during analysis that lasts for multiple days, the system needs to be restarted reliably without damaging the carefully cultured samples Or affect the analysis results. Absolute encoders support continued work when power is restored.
Since the absolute encoder outputs a digital signal, it is compatible with a variety of communication protocols and buses, including BiSS, synchronous serial interface (SSI), DeviceNet, Profibus, Modbus, CANopen, and many other communication protocols based on Ethernet. Without suitable feedback equipment, even the best positioning components in the world will not help. According to the application characteristics, choosing the right encoder can realize the ideal solution. Original equipment manufacturers and machine tool manufacturers need to understand the various characteristics of incremental encoders and absolute encoders, and compare them with application requirements, so that they can be planned and budgeted to have the required performance and service life Product or system.
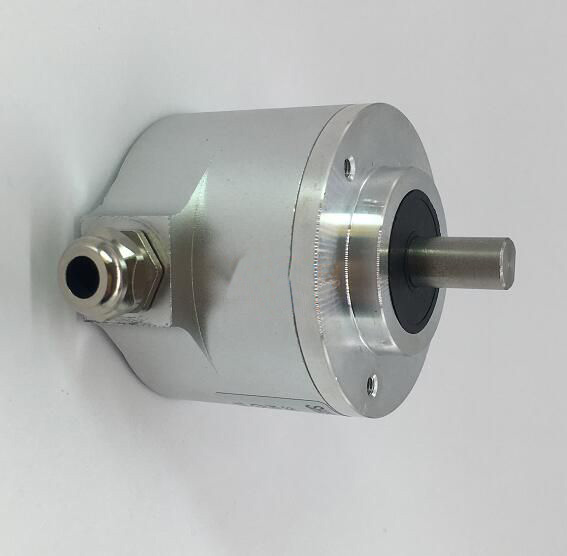
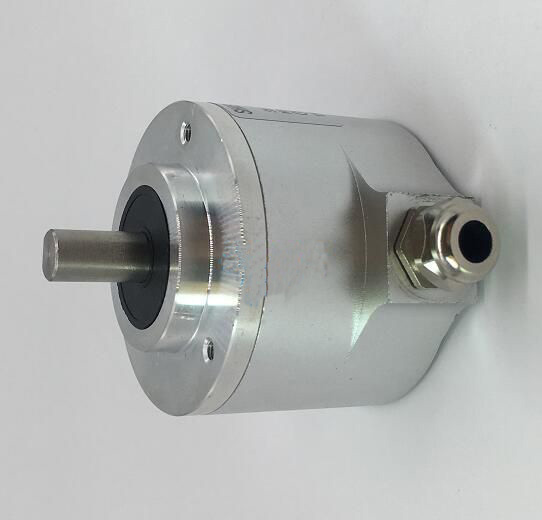
The above-mentioned definition of "absolute" for absolute encoders must not use confusingly "absolute encoders" or "false absolute multi-turn encoders" under the requirements of high-speed and safety applications. ", and must use a true absolute value encoder or an absolute value true multi-turn encoder, and anything that does not rely on counting (no matter internal or external, with or without batteries), all positions are independent, unique and absolute To ensure the absolute reliability and high-speed accuracy of the data. When you select and use an absolute encoder, please make sure whether its internal is the "absolute encoding" introduced above to ensure the absolute effectiveness of the use.