Working principle of absolute encoder_selection of absolute encoder
Working principle of absolute encoder_selection of absolute encoder
Working principle of absolute encoder_selection of absolute encoder
Working principle of absolute encoder
(1)The absolute rotary photoelectric encoder is shown in Figure 4-13. The absolute encoder determines the uniqueness of each position by the mechanical position. It does not need to be memorized, does not need to find a reference point, and does not need to keep counting. When does it need to know the position , When to read its location. In this way, the anti-interference characteristics of the encoder and the reliability of the data are greatly improved, and it has been more and more widely used in angle and length measurement and positioning control of various industrial systems.
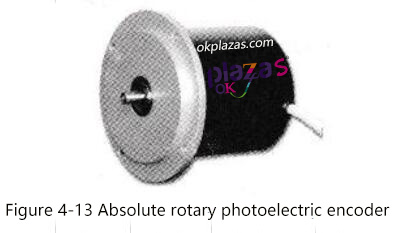
(2) There are many engraved lines on the optical code disc of the absolute encoder, and each engraved line is arranged in order of two lines, four lines, eight lines, sixteen lines..., so that at each position of the encoder, through reading The open and dark of each engraved line obtain a unique binary code (Gray code) from 20 to 2n-1, which is called an n-bit absolute encoder. Such an encoder is determined by the mechanical position of the encoder, and it is not affected by power failure or interference.
(3) Since absolute encoders are significantly better than incremental encoders in positioning, they have been increasingly used in industrial control positioning. Absolute encoders have high precision and a large number of output bits. If parallel output is still used, each output signal must be well connected. For more complex working conditions, it must be isolated, and the number of connecting cables will be large. Many inconveniences and reduced reliability, therefore, the absolute encoder generally selects serial output or bus type output when outputting multiple digits.
Precautions for selection of absolute encoder
One. The conventional shape of absolute encoder: 38MM, 58MM, 66MM, 80MM.100MM.
Two. Absolute encoders are divided into: single-turn and multi-turn.
three. According to the principle, the absolute encoder is divided into: magnetic absolute encoder, photoelectric absolute encoder
Four. Absolute encoder outlet methods are divided into: side outlet, rear outlet
Fives. Absolute encoder shafts are divided into: 6MM, 8MM, 10MM, 12MM, 14MM, 25MM.
Six. Absolute encoders are divided into: shaft, blind hole, and through hole.
Seven. The protection level of absolute encoder is divided into: IP54-68.
Eight. B. Absolute encoder installation methods are divided into: clamping flange, synchronization flange, clamping belt synchronization flange, blind hole (spring leaf, hold tight), through hole (spring leaf, key pin)
Nine. Absolute encoder accuracy is divided into: single-turn accuracy and multi-turn accuracy, which add up to the total accuracy, which is the usual number of bits (regular 24 bits, 25 bits, 30 bits, 32 bits...).
Ten. Absolute encoder communication protocol baud rate: 4800~115200 bit/s, the default is 9600 bit/s. Refresh cycle is about 1.5ms
11. Absolute encoder output optional: SSI, 4-20MA, profibus-dp, DEVicenet, parallel, binary code, BiSS, ISI, CANopen, Endat and Hiperface, etc.