A variety of applications of Pepperl + Fuchs sensor cables
A variety of applications of Pepperl + Fuchs sensor cables
More than 150 years ago, communication pioneers tried boldly and costly to establish a telegraph line between North America and Europe. In the process, an astonishing number of cables were laid thousands of kilometers under the sea. Despite many challenges, they successfully established the connection, but only a few weeks later, it was damaged, partly because of cable limitations. Like these pioneers, Pepperl+Fuchs produces cables each year with lengths of thousands of kilometers, and these cables can meet almost all challenges. Today, let us learn more about Pepperl+Fuchs' 20-year connection experience and the various applications of Pepperl+Fuchs sensor cables.
Reliable connection, originality
Whether it is machine building, welding, logistics, construction machinery or process industry, "powerful sensor technology requires strong and reliable connection technology", explained Mr. Jürgen Chrobak, managing director of Pepperl+Fuchs Group Hungary. In fact, seemingly simple sensor accessories are also an important part of automation technology. The failure of just one connector may cause the entire factory to fail and shut down, at a huge price. "Saving the cost of connecting parts often leads to increased maintenance costs," said Mr. Roland Gubbels, Business Manager of Pepperl+Fuchs Connecting Parts.
To protect users from these risks, in Veszprém, Hungary, more than 200 Pepperl+Fuchs employees have developed, tested and produced high-quality automated cable assemblies for 20 years. What needs to be considered when developing connection technology? "As in many other areas, there are some challenges here. On the one hand, cables and connectors are highly standardized, which means they are compatible with sensors regardless of the manufacturer. At the same time, Pepperl+Fuchs wants to provide more than just standardization Products," Mr. Gubbels said. In order to achieve this goal, Pepperl+Fuchs attaches great importance to more details, such as vibration protection, knurled nuts designed for safe installation, innovative snap-on design to protect the cable layer, and 360-degree shielding.
"We clearly understand the needs of our customers-which cable should be used for which application. Our years of experience enable us to provide targeted, industry-specific solutions," Mr. Chrobak said.
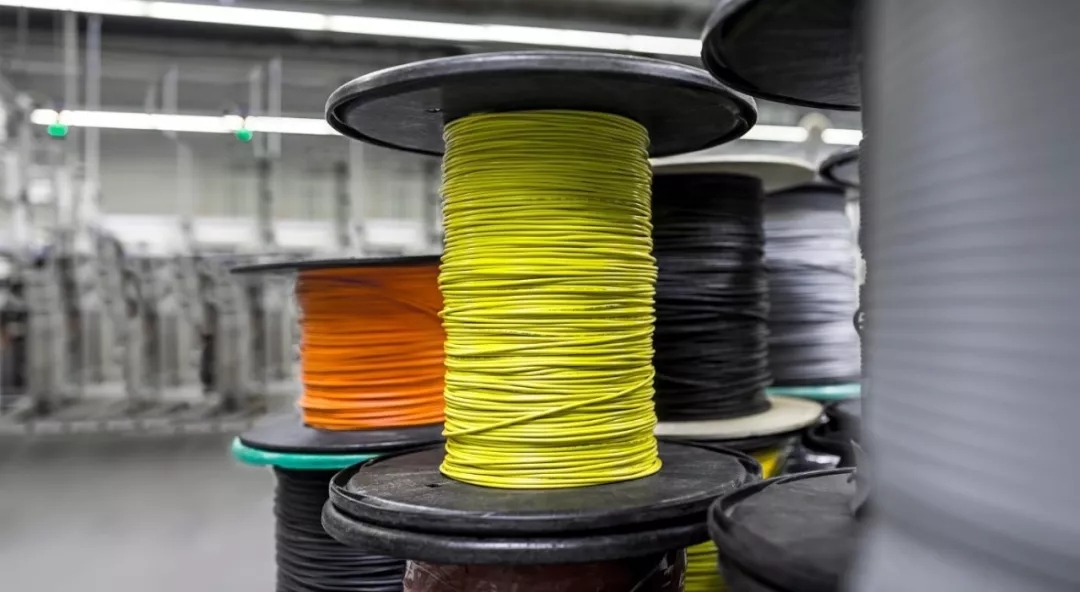
Food industry: cleaner and sanitary
In the food industry, safety and hygiene are the top priority. In any case, products and packaging will not be contaminated by contact with machine parts. The connector design plays a vital role: the surface must be smooth, easy to clean, and conform to the guidelines of EHEDG (European Hygienic Engineering and Design Organization). The accessories are made of stainless steel to ensure that no food sticks to the surface. High-quality connections must also withstand intensive cleaning procedures and chemical reagents. "That's why Pepperl+Fuchs's 4-pin and 5-pin M8 and M12 connectors can meet the strict requirements for spray and contact areas. They are also PVC and halogen-free, comply with FDA standards, and are certified ECOLAB. This combination ensures Cleanliness, and can be completely hygienic and safe during the cleaning of the machine and components," said Mr. Gubbels.
Robot industry: durable and highly flexible
Unlike food production, certain industries involve hazardous work. For these tasks, robots are used to perform millions of repetitive actions. In some areas, the robot movement may be extremely bending and rotating. In order to prevent production downtime, the connector must ensure constant power and data transmission between the robot and the automation system during use. "Pepperl+Fuchs PUR-R cables can be twisted ±360° more than ten million times per meter. They ensure that every component in a highly automated production process can work reliably, withstand high temperatures, and is resistant to oil and chemical corrosion. PUR- R cables meet all these requirements because they are very flexible, suitable for drag chains, and can be twisted ten million times," Mr. Gubbels explained.
For the automotive industry: resistant to welding spatter
On the other hand, if cables are used in an environment with fumes and welding slag, they must be able to work reliably, even in the presence of huge direct or indirect heat. Fortunately, Pepperl+Fuchs has a long history as a supplier of automotive manufacturing and is very familiar with the strict requirements of welding applications. PUR-A cables are designed for areas where the cable is in contact with welding spatter and requires a high degree of flexibility. However, in an extremely hot environment, such as a body shop, the cable may come into contact with the spark stream, so special cables are required. "If the cable in your application is close to the welding process, you can choose POC coated cable. High mechanical strength, resistance to continuous working temperature up to 150 °C, resistance to welding spatter, these cables can be used for high temperature and welding where other cable types cannot work. Area where slag splashes," Mr. Gubbels said of this high-resistance special cable.
Special for construction machinery: more optimized design
Cables are not only exposed to extreme conditions in automobile manufacturing plants, but are also used in factory machinery and equipment. "With the introduction of the professional MEC (Mobile Device Connectivity) product portfolio, we are reducing the distance between the circular plug connector and the "car world". Through our mature sealing design, we provide robust connectors for mobile devices. Gubbels Mr. said. It is based on the tried and tested connectors from Deutsch, AMP and TE Connectivity, which have been optimized by Pepperl+Fuchs for construction machinery applications. "Mobile device connector housings are overmolded to withstand harsh environments and provide long-lasting Protection, and can work in the temperature range of -50 to 105 °C. In addition, their slim design minimizes the space required for operation, and innovatively designed protective cable layers to connect reliably without using additional accessories," Gubbels added.