Analog encoder
Analog encoder
Analog encoders are also called current encoders and voltage encoders, which are divided into single-turn and multi-turn. Encoder Analog encoder can be externally set, multi-purpose, multi-function, directly corresponding to single-turn multi-turn angle, multi-turn length, rotation and translation speed measurement. 4mA corresponding value, 20mA corresponding value can be set and fine-tuned arbitrarily; direction setting; external setting line setting preset position, easy installation, no need to change. The internal absolute value photoelectric code disc, fully digitalized value, 1/4096 high linearity, the signal has no temperature, mechanical influence, signal interference zero drift is very small, IP65 waterproof, oil-proof and shock-proof.
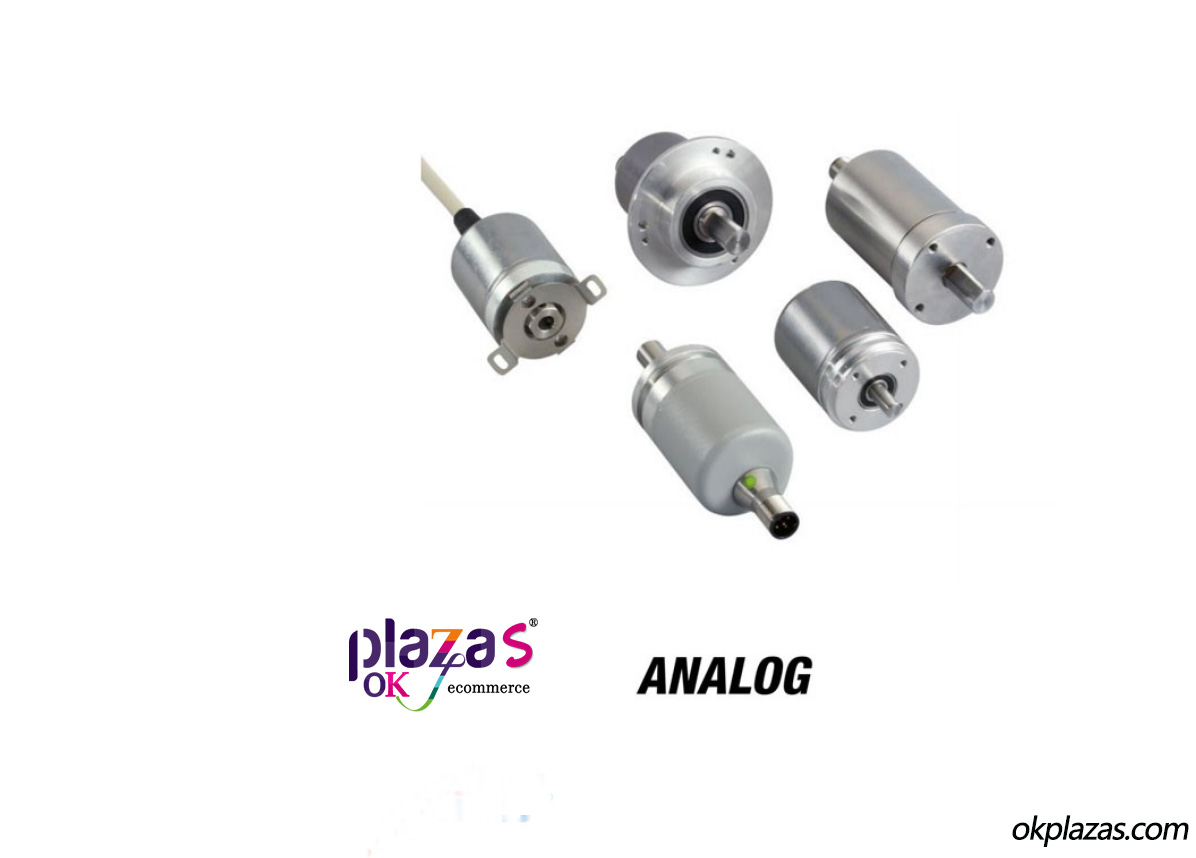
The analog encoder is divided into single-turn and multi-turn according to the number of turns. The external dimensions are 38MM, 58MM, and 80MM. The wire-out method is divided into side-out and rear-out. It can be used in trucks, buses, vehicle engineering machinery, mining equipment, elevators, elevators, medical equipment, water conservancy engineering, wind energy, solar photovoltaic industry, mobile platforms, offshore and communication engineering and other fields.
Examples of commonly used analog encoders:
Brand: POSITAL Germany Bosite
Model: UCD-AC005-0413-D10D-PAM
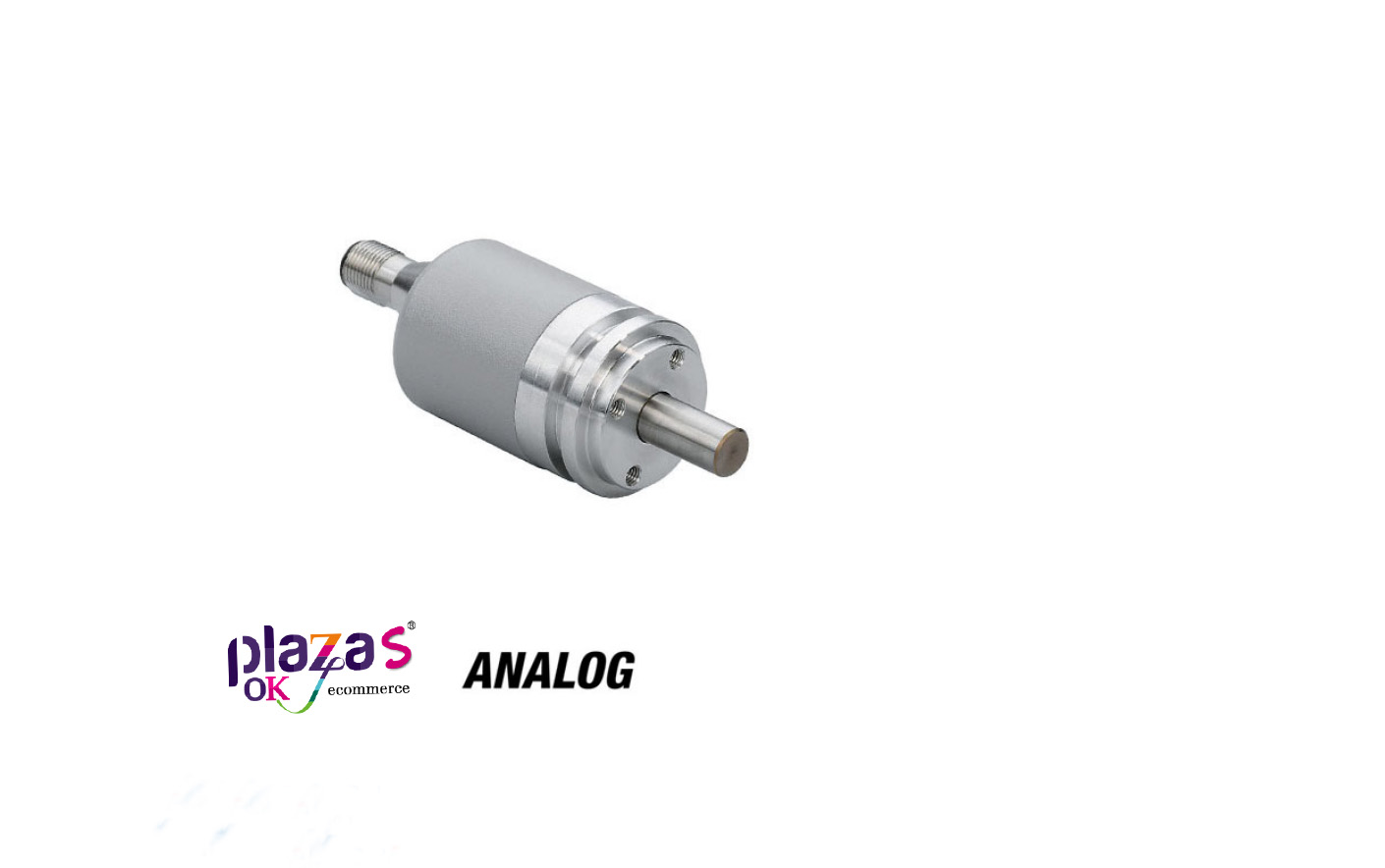
Electrical data
Power supply voltage 8 – 32 VDC
Power consumption usually @24V (no load) 20mA
Start-up time <500 ms
Load resistance 500 Ω
Analog quantity accuracy @ 20 mA = ±20 µA (under normal power supply conditions)
Linearity 0.15%
Setup time 32ms (jump from minimum to maximum)
Reverse polarity protection
Short circuit protection
EMC: emission interference DIN EN 61000-6-4
EMC: Anti-interference DIN EN 61000-6-2
MTTF 240.8 years @ 40 °C
sensor
Technology Magnetic
Single-turn resolution 13 bits
Resolution multiturn 4 bits
Multi-turn technology Self-generated magnetic pulse counter (no battery and gear set required)
Accuracy (INL) ±0.0878°(≤12bits)
Detection signal (default value) When rotating counterclockwise (facing the axis), the value decreases
Certification Certification/lifetime Code system code Analog current signal 4 – 20 mA
Period basic sensor <100 µs
Minimum measuring range 0 – 22.5°
Output resolution The highest resolution in the full range is 13 bits (graded rotation-when the measurement range is less than 90 degrees, the resolution will be below 13 bits)
Multi-turn range 16 bits (default setting). Users can use the set range function to measure up to 65536 circles (you can also use the UBIFAST tool to change the circle
number)
Environmental specifications
Enclosure protection level (shaft) IP68/IP69K
Enclosure protection level (enclosure) IP68/IP69K
Operating temperature -40 °C (-40 °F)-+85 °C (+185 °F)
Humidity 98% relative humidity, non-condensing
Mechanical data
Shell material steel
Shell coating Cathodic anti-corrosion protection (> 720 hours salt spray resistance test)
Flange form Synchro flange, ø 36 mm heavy duty
Flange material aluminum
Type of shaft Solid shaft, length = 20 mm
Shaft diameter ø 10 mm (0.39")
Shaft material stainless steel V4A (1.4112, 440 B), reinforced
Maximum shaft load 180 N axial, 180 N radial
Minimum mechanical life 10 (180 N / 180 N), 15 (150 N, 150 N), 30 (100 N / 100 N)
Friction torque ≤ 5 Ncm @ 20 °C, (7.1 oz-in @ 68 °F)
Maximum mechanical speed ≤ 6000 1/min
Impact resistance ≤ 200 g (half sine 11 ms, EN 60068-2-27)
Durable impact resistance ≤ 30G (6 millisecond half-sine wave, EN60068-2-29)
Vibration resistance ≤ 30 g (10 Hz – 1000 Hz, EN 60068-2-6)
Length 56 mm (2.20")
Weight 210 g (0.46 lb)
Electrical connections
Connection direction Axial
Interface M12, male, 5-pin, A size