How to choose suitable encoders for different motors
How to choose suitable encoders for different motors
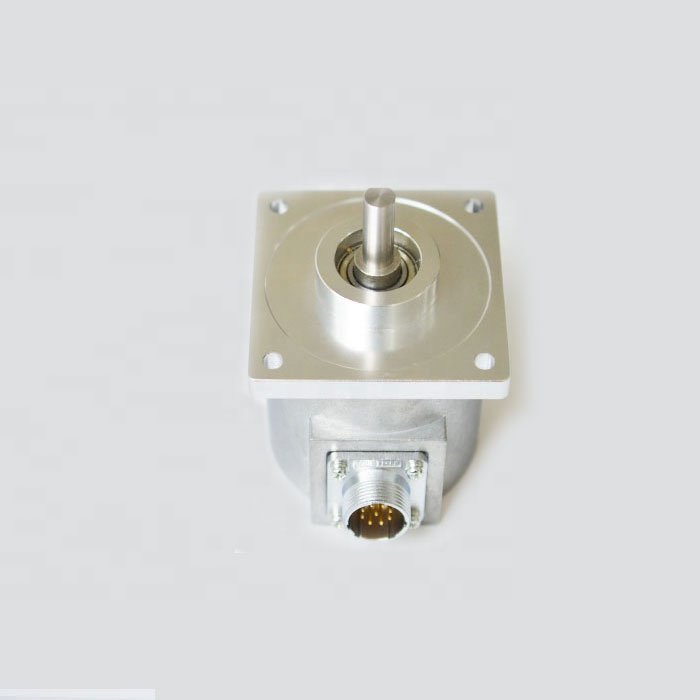
1 Mechanical appearance
2 Mechanical speed (Speed)-the structural design of the encoder makes it the maximum rotational speed that it can reach and withstand, which is expressed as the rotational speed that can be achieved within one minute-rpm; (so the maximum working speed of the encoder should be taken into account at the same time The mechanical speed and response frequency of the encoder and the switching frequency of the subsequent receiving device of the encoder)
3 Shaft Dimension—The shaft diameter of the solid shaft of the encoder is 6 mm*, 8 mm, 10 mm*, 12 mm, etc., and the shaft diameter of the hollow shaft is 8 mm, 10 mm, 12 mm*, and large diameter 20 ~50mm* etc. The ones with * are conventional specifications.
4 Resolution (Resolution)—The number of signals output per revolution of the encoder in a single revolution is called resolution, also known as resolution, or directly called the number of lines. Generally, the number of encoder output lines is 5~10000 lines . Such as: 1024ppr, 2048ppr, etc.
5 Working power supply (Power-Vcc)—Encoders generally have only two voltages, one is DC9~36V, the other is DC5V standard voltage
6 Working temperature (Temperature)—The maximum and minimum working temperature of the encoder represents the internal mechanical [coordination and composition of the encoder, as well as the level of electronic components. The better working temperature of the encoder is from -40 to 100°C. In fact, under low temperature conditions, the internal electronic parts and external cables and sealing characteristics are restricted.
7 Degree of protection
8 Encoder output signal
9 Signal form