Industry 4.0, sensors have undergone what changes
Industry 4.0, sensors have undergone what changes
Integration from sensor to data platform
Today, sensors provide more than just data. Using the correct interface and protocol, valuable additional information can also be transmitted to the platform. Through appropriate interfaces, communication modules and data (language) protocols, all sensor data can be provided in the cloud system or local data platform. Even without understanding the transmission technology, the data information of the sensor can be processed and abstracted into a communication channel.
Sensors convert physical effects into electrical signals or digital information so that they can be processed further. In fact, sensors act as the sensory organs of factories and machines, and are the cornerstone of the Industry 4.0 scene.
In addition to pure data, modern sensors can also provide a large amount of valuable additional data, such as the characteristics or status of the sensor itself. It is also possible to modify sensor related parameters online to make it perfectly suitable for different applications. Two-way communication and data protocol are necessary, which can transmit relevant parameters online to the sensor and receive measurement data information from the sensor. Interfaces and protocols must strictly follow applicable standards in order to achieve error-free use of products from different manufacturers. IO-Link has become the preferred interface for the "last 1 centimeter" in sensor technology; and Ethernet-based technologies such as EtherCAT, PROFINET, and EtherNet/IP can be used for more complex devices.
Pepperl+Fuchs Group has registered and used the Sensorik4.0® trademark to describe this concept and design corresponding products based on it. When evaluating the process data of sensors, the real-time nature of data processing must be considered in the application of closed control loops. In this case, because of strict real-time requirements, PLC hardware must be perfectly combined with data communication. For sensor additional data information, the real-time data processing requirements are not high. But these additional data information must be able to be recorded, stored and processed for a long time. In addition to signal transmission paths, parallel data paths must be constructed to reach the data platform. For this, we use an edge gateway.
The edge gateway can not only establish communication with sensors, actuators, and PLC through the control module, but also establish a connection with the data platform. This is achieved by using a communication protocol that supports the publish/subscribe mechanism, such as MQTT, AMQP, or OPC/UA with Pub/Sub extension. The data platform can run on the local network inside the factory, or can be used as an online cloud platform solution. These platforms have structured databases for storing sensor data; and provide various application interfaces for data access. Through the application programming interface (API), sensor data can be accessed and transmitted to the platform, which is unique to each system. In order for the edge gateway to connect to this platform, it must also use the API of this platform.
Pepperl+Fuchs Group has created a subsidiary, Neoception, to provide high-quality services for this type of software, so that customers have the greatest flexibility in choosing a data platform. Neoception combines the expertise of sensors and IT technology and provides interconnection services for all cloud systems available on the market. At the sensor/actuator level, there are a series of different communication protocols, but there is no unified semantic set. For each type of field device, appropriate commands must be generated according to specific rules and interpreted according to these rules. The specific attributes of the field device can be found in the description file ("device description", DD for short) provided by the manufacturer with the device. According to different technologies, various description files of different formats (EDDL, GSD, GSDML, IODD, etc.) are used.
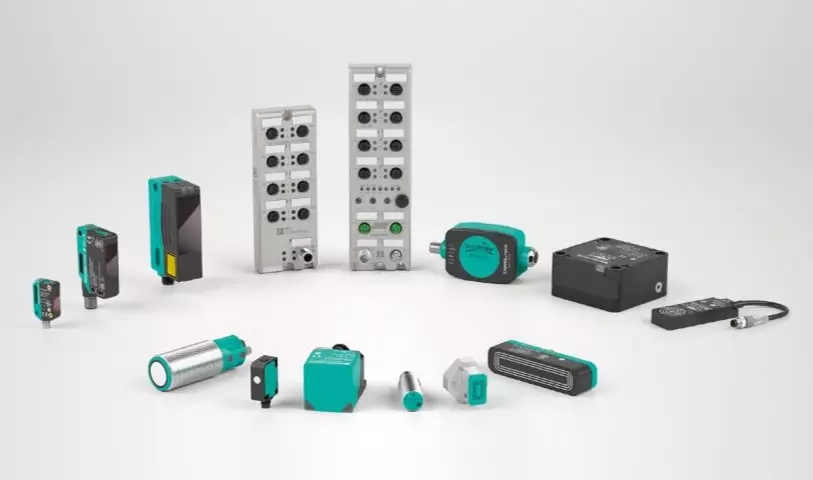