Pepperl + fuchs encoder incremental and absolute value of the two differences
Pepperl + fuchs encoder incremental and absolute value of the two differences
Pepperl + fuchs encoder incremental and absolute value of the two differences
Pepperl+Fuchs encoder is one of the products of the world-famous German Pepperl+Fuchs brand.
Pepperl+Fuchs encoders are widely used in industrial fields, such as controlling system speed and positioning in the steel industry, controlling the position of cutting paper in the printing industry, measuring the size of packaging paper in the packaging industry, etc.
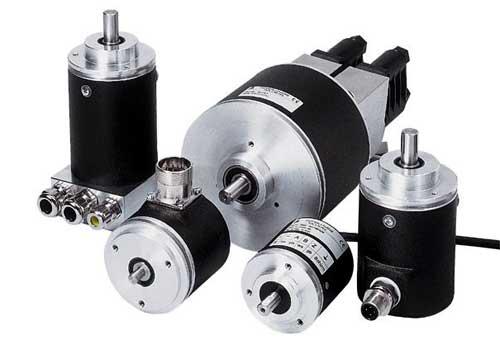
Pepperl+Fuchs encoder
Pepperl+Fuchs encoders are generally divided into incremental and absolute types. What is the difference between them? We can know through the following comparison.
Pepperl+Fuchs incremental encoder provides a fixed number of pulses per revolution, and the speed is calculated by the number of pulses measured per unit time. In order to measure angle and position, it is usually counted from a starting reference point. The dual-channel output encoder has two signals with a phase difference of 90 degrees. This allows the controller to determine the direction of rotation and realize the function of bidirectional position measurement.
Pepperl+Fuchs absolute encoder provides a unique encoded digital value for the position of each axis, that is, each position change generates a fixed code. Especially in the application of positioning control, the absolute value encoder reduces the calculation task of the electronic receiving equipment, thereby saving complex and expensive input devices. Moreover, the absolute rotary encoder has a power-off memory function, that is, the current position is memorized after the power is off, and there is no need to search for the reference position when the power is restored-when the machine and the power supply or the power supply fails, then the power is turned on. Back to the position reference point, the current position value can be used. Functionally, it is divided into single lap and multiple laps. There are different interfaces, etc.
It can be seen that there is the biggest difference between Pepperl+Fuchs incremental encoder and absolute encoder: In the case of an incremental encoder, the position is determined by the number of pulses calculated from the zero mark, while an absolute encoder The position of is determined by the reading of the output code. In a circle, the reading of the output code of each position is unique; therefore, when the power is disconnected, the absolute encoder is not separated from the actual position. If the power is turned on again, the position reading is still current and valid; unlike incremental encoders, you must search for the zero mark.