Pepperl+Fuchs helps the aviation equipment manufacturing industry leap into the cloud!
Pepperl+Fuchs helps the aviation equipment manufacturing industry leap into the cloud!
Pepperl+Fuchs helps the aviation equipment manufacturing industry leap into the cloud!
At the time of the annual Spring Festival travel season, "the world's largest population migration", whether it is going home for reunion or going on vacation, traffic problems always affect people's hearts. Civil aviation predicts that the number of passengers sent during the Spring Festival will hit a record high in the Spring Festival. The transportation mode of "passing through the clouds" is becoming more and more popular. The number of people who choose to travel by air is increasing rapidly, and the aviation industry is experiencing vigorous development. When you get on the plane for a few hours, you have already found yourself thousands of miles away, and the plane can take us almost all over the world.
Large passenger aircraft manufacturing, an integrated system engineering, is called "the crown of modern industry." Today, we approached the manufacture of large aircraft together and discovered Pepperl+Fuchs’ unique innovative scanning technology and "cloud technology". How can we help the manufacture of large aircraft? While ensuring flight safety, it provides passengers with a comfortable flight experience.
In major airports in the world, a large plane takes off almost every second, bringing passengers and their luggage to all parts of the world. But people don’t just fly to save time: it’s still considered the safest mode of transportation, and airplanes often need to be very tightly controlled and tested. Even the tiny components must be ensured that there is no failure, because in the air, the consequences of any failure may be fatal. This applies to a large number of electronic components installed on and in the aircraft, as well as various parts of the overall aircraft design.
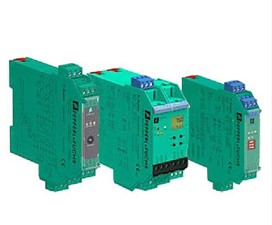
No easy task, extremely challenging
Before a "behemoth" made of steel weighing hundreds of metric tons can fly into the sky, it must be manufactured with the most advanced engineering technology and the highest precision, and must meet a variety of conditions to form the aerodynamic power required for aircraft flight. Therefore, the design must be accurate to ensure that the condition of the aircraft is nearly perfect. For example, external cracks and dents can have catastrophic effects on the aerodynamics of the aircraft, and these potential hazards should be avoided at all costs.
The huge shape of the aircraft presents special challenges. Individual parts such as wings are several meters long, and the fuselage is longer, not to mention the huge engine. This makes the assembly of every aircraft component a very challenging task and requires millimeter-level accuracy. These advanced technologies can scan the overall height, width and length of large parts, providing important support for aircraft manufacturers and maintenance personnel in the correct assembly, quality control and regular inspections.
Piercing eyes, meticulous
Pepperl+Fuchs provides solid technical support for this challenge: the combination of multiple 2D LiDAR scanner sensors can accurately detect and assemble large aircraft and their components. The calibrated sensors are located in different positions and can record target data from different angles. Combine all the data from the 2-D LiDAR scanner to form a three-dimensional point cloud to create an accurate digital image. Workers can use this image to accurately identify the structure and positioning of components. Especially when the machine and parts need to be accurately positioned to avoid collisions when assembling various components.
Before the various parts of the aircraft are combined to form a whole, a system composed of multiple 2-D scanners escorts them. After all, it is not uncommon for aircraft components to be produced in different locations: for example, a German-made fuselage, French or American-made wings. In order to ensure that the components can be assembled together during the final assembly, the scanned data and the generated 3-D images can be compared with preset values and models at any time.
Cloud technology, connect the world
The data collected by multiple sensor systems can immediately provide the standard data format on the Pepperl+Fuchs subsidiary NeoNeon Cloud, which means that the three-dimensional images of the aircraft or its various components can be used anywhere in the world, also in the context of distributed production facilities. Now it's not just wing manufacturers who can compare their designs with the original. Manufacturers located in other component production areas can also access the scanned data, and can use the 3D data for further processing to optimize components, and even form the basis for their own production.
Copy success, improve efficiency
Those successful experiences in aircraft manufacturing can also be used for reference in many other application fields. Pepperl+Fuchs integrates multiple smart sensors to form a scanning technology that can not only capture large components and the overall space, but also accurately scan and capture small targets, larger targets, machines and even people. The three-dimensional cloud of accumulated data points can be processed immediately by NeoNeon Cloud. They can be used all over the world, directly used in production, and even customized production of "one batch" can be achieved. This can flexibly meet and implement customer wishes and requirements, and enable companies with distributed production facilities to optimize plant utilization and increase efficiency.