Pepperl + Fuchs incremental rotary encoder series ENI58IL- Blu-ray technology
Pepperl + Fuchs incremental rotary encoder series ENI58IL- Blu-ray technology
Pepperl + Fuchs incremental rotary encoder series ENI58IL- Blu-ray technology
Photoelectric switch:
The photoelectric switch is the abbreviation of the photoelectric proximity switch. It utilizes the shielding or reflection of the light beam by the detected object, and the circuit is connected by the synchronization loop to detect the presence or absence of the object. The object is not limited to metal, all objects that can reflect light (or block light) can be detected. The photoelectric switch converts the input current into a light signal on the transmitter, and then the receiver detects the target object according to the intensity or presence of the received light. The common photoelectric switch smoke alarm in the security system is often used in the industry to count the number of movements of the robotic arm.
Photoelectric switch model:
The photoelectric switch is a kind of sensor, which converts the change of the intensity of light between the transmitting end and the receiving end into the change of current to achieve the purpose of detection. Since the output circuit and input circuit of the photoelectric switch are electrically isolated (ie, electrically insulated), it can be used in many occasions. A new generation of photoelectric switch devices manufactured using integrated circuit technology and SMT surface mounting technology has intelligent functions such as delay, widening, external synchronization, anti-interference, high reliability, stable working area and self-diagnosis. This novel photoelectric switch is an active photoelectric detection system electronic switch that uses pulse modulation. The cold light source used in it includes infrared light, red light, green light and blue light, etc., which can be non-contact and rapid without damage And control the state and action of various solid, liquid, transparent, black, soft, smoke and other substances. It has the advantages of small size, multiple functions, long life, high precision, fast response speed, long detection distance and strong resistance to optical, electrical and magnetic interference.
Photoelectric switch manufacturers:
Use optical elements to change the light beam in the middle of the propagation medium; use the light beam to reflect the object; make the light beam return instantaneously after a long distance. The photoelectric switch is composed of three parts: transmitter, receiver and detection circuit. The transmitter is aimed at the target to emit a beam, and the emitted beam generally comes from a light emitting diode (LED) and a laser diode. The beam is emitted continuously, or the pulse width is changed. The radiation intensity of the pulsed beam has been selected many times during the launch, and it moves towards the target without indirection. The receiver is composed of a photodiode or phototransistor. In front of the receiver, there are optical components such as lens and aperture. Behind it is the detection circuit, which can filter out the effective signal and apply the signal.
Working principle of photoelectric switch:
After the modulated pulse generated by the oscillation circuit passes through the reflection circuit, the light pulse is radiated from the luminous tube GL. When the measured object enters the range of the light receiver, the reflected light pulse enters the photosensitive transistor DU. The photoelectric switch demodulates the optical pulse into an electrical pulse signal in the receiving circuit, then is amplified by the amplifier and synchronized gating and shaping, then the interference is eliminated by digital integration or RC integration, and finally the driver is triggered by a delay (or no delay) Output photoelectric switch control signal. Photoelectric switches generally have good hysteresis characteristics, so even if the detected object is swayed in a small range, it will not affect the output state of the driver, so that it can be kept in a stable working area. At the same time, the self-diagnostic system can also display the light receiving state and stable working area to monitor the work of the photoelectric switch at any time.
Types of photoelectric switches:
Amplifier separation type is to separate the amplifier and the sensor, and use the special integrated circuit and the mixed installation craft to make, because the sensor has the characteristics of ultra-small and multi-variety, and the amplifier has more functions. Therefore, this type adopts the terminal block connection method and can be used for both AC and DC power supplies. It has the function of on and off delay, can set the light and sound switch, can control 6 kinds of output states, and has two output modes of contact and level.
The built-in type of amplifier integrates the amplifier and the sensor. It is made by ASIC and surface mounting technology, and works with DC power supply. Its response speed situation (there are two kinds of 0.1ms and 1ms), can detect small and high-speed moving objects. Changing the polarity of the power supply can switch between bright and dark movement, and can set the self-diagnostic stable work area indicator. Both voltage and current output modes can prevent mutual interference, which is very convenient in system installation.
The built-in power supply unit integrates the amplifier, sensor and power supply device, and is made with ASIC and surface mounting technology. It generally uses AC power, which is suitable for replacing contact type limit switches at the production site and can be directly used for strong current control circuits. You can also set self-diagnostic and stable working area indicator lights by yourself. The output is equipped with SSR solid-state relay or relay normally open and normally closed contacts to prevent mutual interference and can be installed tightly in the system.
Photoelectric switch price:
Strong light source: The photoelectric switch can generally work stably when the ambient illuminance is high. However, it should be avoided that the optical axis of the sensor faces strong light sources such as sunlight and incandescent lamps. When the angle between the optical axis of the sensor (receiver) and the strong light source cannot be changed, a light-shielding plate or a long light-shielding tube can be installed around the sensor.
Mutual interference: MGK series of new photoelectric switches usually have the function of automatically preventing mutual interference, so there is no need to worry about mutual interference. However, when several groups of HGK series through-beam infrared photoelectric switches are installed in parallel and close to each other, they should prevent adjacent groups and mutual interference. The most effective way to prevent this kind of interference is to set the emitter and the receiver crosswise, and open the group distance when more than 2 groups. Different frequency models can also be used.
The effective way of HGK series reflective photoelectric switch to prevent mutual interference is to open the interval. And the farther the detection distance is, the larger the interval should be, and the specific interval should be determined according to the debugging situation. Of course, models with different operating frequencies can also be used.
Photoelectric switch wiring diagram:
The slot photoelectric switch is usually a standard U-shaped structure, and its transmitter and receiver are located on both sides of the U-shaped groove and form an optical axis. When the detected object passes through the U-shaped groove and blocks the optical axis, the photoelectric switch The detected switch signal is generated. The slot-type photoelectric switch is safe and reliable for detecting high-speed changes and distinguishing transparent and semi-transparent objects.
Optical fiber photoelectric switches use plastic or glass optical fiber sensors to guide light, so as to realize the detection that the detected object is not in the vicinity. Generally, fiber optic sensors are divided into through-beam type and diffuse reflection type.
related suggestion:
Photoelectric switch
Pepperl+Fuchs
liquid level sensor
Ultrasonic sensor
Surge protector
Safety barrier
Photoelectric switch articles:
The ENI58IL incremental rotary encoder series launched by Pepperl+Fuchs this time introduced the Blu-ray code disc scanning technology ("BlueBeam"Technology) for the first time in the industry. Standard industrial rotary encoder products based on this technology can still achieve unparalleled high-precision performance when the working speed is as high as 12000RPM. These are all due to the blue LED transmitter and corresponding receiving optocoupler components, combined with high-performance sensor chips, to achieve efficient use of light.
New standard for signal quality of incremental rotary encoder
"Compared with the long-wave infrared light used in traditional rotary encoders, the blue light emitted by the blue LED has a shorter wavelength, and can achieve clearer fringe images under the same code disc grating line width," Pepperl+Fuchs Global Stefan Horvatic, product manager, explained. Based on the innovation of this functional principle, the high reference signal quality that users expect is achieved. "Blu-ray code disc scanning technology makes the phase difference and pulse width fluctuation amplitude of the A and B channel output signals far less than 10%" Horvatic made a supplementary explanation. The achievable signal quality is more than twice that of the incremental rotary encoder of traditional infrared light technology. At the same time, because high-frequency sampling is not susceptible to interference, the Blu-ray technology encoder can still maintain a stable signal in the case of strong mechanical shock and vibration.
Another technical advantage of the ENI58IL encoder is that it additionally uses a code disc calibration assembly process that exceeds standard manufacturing; in its production process, in order to ensure the precise insertion of the code disc, it must be calibrated under a microscope and other parameters. This process not only improves the absolute accuracy of product application, but also prevents the non-negligible performance loss caused by subtle deviations to customers.
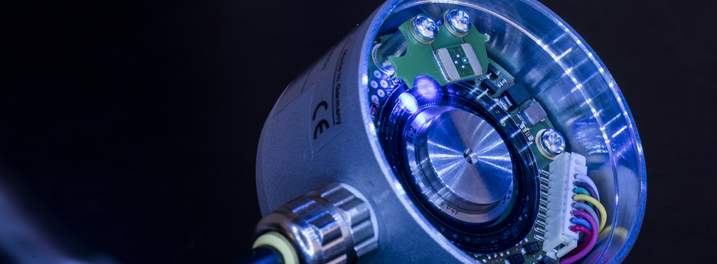
The blue LED transmitter and corresponding receiving optocoupler components, together with high-performance sensor chips, realize the efficient use of light
Incremental rotary encoder with bearing lock design
ENI58IL series encoders, in addition to the introduction of blue light technology to achieve high-precision measurement, also made great efforts in reliability and durability: bearing lock design, protect ball bearings, can withstand greater axial load; special EMC protection circuit, Avoid encoder damage caused by strong electromagnetic interference. "At present, most of the rotary encoders sold in the world generally only meet the minimum requirements of the CE standard. Our test standards are four times better than the conventional standard levels, ensuring that the products can operate accurately and reliably under severe and challenging application conditions. "Mr. Horvatic said.
Multiple performance advantages, all in one
Based on the single-chip modular production process, the ENI58IL incremental rotary encoder perfectly integrates a very wide range of characteristics and advantages; its shaft type (solid shaft, hollow shaft, semi-hollow shaft), flange (clamping flange, servo Flange, square flange), electrical connection (radial, axial cable or M23/M12 connector) have a variety of styles to choose from. "The emergence of ENI58IL, a precision-designed industrial standard encoder series, has replaced the traditional special encoder equipment to meet special applications," Mr. Horvatic emphasized.
List of outstanding features of Pepperl+Fuchs ENI58IL incremental rotary encoder
1. Blu-ray code disc scanning technology: even at the limit speed of 12000RPM, it can still provide you with unparalleled application accuracy
2. Anti-strong shock and vibration, EMC enhanced circuit design, provide unparalleled reliability for system process control
3. The bearing is locked and designed for heavy load to resist greater shaft load and effectively extend the service life of the product
4. Diversified connection methods such as shaft type, flange, electrical, etc., can provide proprietary and optimized solutions for various applications