Pepperl + Fuels launches a new flexible and efficient PMI sensor positioning system
Pepperl + Fuels launches a new flexible and efficient PMI sensor positioning system
Pepperl + Fuels launches a new flexible and efficient PMI sensor positioning system
Photoelectric switch:
The photoelectric switch is the abbreviation of the photoelectric proximity switch. It utilizes the shielding or reflection of the light beam by the detected object, and the circuit is connected by the synchronization loop to detect the presence or absence of the object. The object is not limited to metal, all objects that can reflect light (or block light) can be detected. The photoelectric switch converts the input current into a light signal on the transmitter, and then the receiver detects the target object according to the intensity or presence of the received light. The common photoelectric switch smoke alarm in the security system is often used in the industry to count the number of movements of the robotic arm.
Photoelectric switch model:
The photoelectric switch is a kind of sensor, which converts the change of the intensity of light between the transmitting end and the receiving end into the change of current to achieve the purpose of detection. Since the output circuit and input circuit of the photoelectric switch are electrically isolated (ie, electrically insulated), it can be used in many occasions. A new generation of photoelectric switch devices manufactured using integrated circuit technology and SMT surface mounting technology has intelligent functions such as delay, widening, external synchronization, anti-interference, high reliability, stable working area and self-diagnosis. This novel photoelectric switch is an active photoelectric detection system electronic switch that uses pulse modulation. The cold light source used in it includes infrared light, red light, green light and blue light, etc., which can be non-contact and rapid without damage And control the state and action of various solid, liquid, transparent, black, soft, smoke and other substances. It has the advantages of small size, multiple functions, long life, high precision, fast response speed, long detection distance and strong resistance to optical, electrical and magnetic interference.
Photoelectric switch manufacturers:
Use optical elements to change the light beam in the middle of the propagation medium; use the light beam to reflect the object; make the light beam return instantaneously after a long distance. The photoelectric switch is composed of three parts: transmitter, receiver and detection circuit. The transmitter is aimed at the target to emit a beam, and the emitted beam generally comes from a light emitting diode (LED) and a laser diode. The beam is emitted continuously, or the pulse width is changed. The radiation intensity of the pulsed beam has been selected many times during the launch, and it moves towards the target without indirection. The receiver is composed of a photodiode or phototransistor. In front of the receiver, there are optical components such as lens and aperture. Behind it is the detection circuit, which can filter out the effective signal and apply the signal.
Working principle of photoelectric switch:
After the modulated pulse generated by the oscillation circuit passes through the reflection circuit, the light pulse is radiated from the luminous tube GL. When the measured object enters the range of the light receiver, the reflected light pulse enters the photosensitive transistor DU. The photoelectric switch demodulates the optical pulse into an electrical pulse signal in the receiving circuit, then is amplified by the amplifier and synchronized gating and shaping, then the interference is eliminated by digital integration or RC integration, and finally the driver is triggered by a delay (or no delay) Output photoelectric switch control signal. Photoelectric switches generally have good hysteresis characteristics, so even if the detected object is swayed in a small range, it will not affect the output state of the driver, so that it can be kept in a stable working area. At the same time, the self-diagnostic system can also display the light receiving state and stable working area to monitor the work of the photoelectric switch at any time.
Types of photoelectric switches:
Amplifier separation type is to separate the amplifier and the sensor, and use the special integrated circuit and the mixed installation craft to make, because the sensor has the characteristics of ultra-small and multi-variety, and the amplifier has more functions. Therefore, this type adopts the terminal block connection method and can be used for both AC and DC power supplies. It has the function of on and off delay, can set the light and sound switch, can control 6 kinds of output states, and has two output modes of contact and level.
The built-in type of amplifier integrates the amplifier and the sensor. It is made by ASIC and surface mounting technology, and works with DC power supply. Its response speed situation (there are two kinds of 0.1ms and 1ms), can detect small and high-speed moving objects. Changing the polarity of the power supply can switch between bright and dark movement, and can set the self-diagnostic stable work area indicator. Both voltage and current output modes can prevent mutual interference, which is very convenient in system installation.
The built-in power supply unit integrates the amplifier, sensor and power supply device, and is made with ASIC and surface mounting technology. It generally uses AC power, which is suitable for replacing contact type limit switches at the production site and can be directly used for strong current control circuits. You can also set self-diagnostic and stable working area indicator lights by yourself. The output is equipped with SSR solid-state relay or relay normally open and normally closed contacts to prevent mutual interference and can be installed tightly in the system.
Photoelectric switch price:
Strong light source: The photoelectric switch can generally work stably when the ambient illuminance is high. However, it should be avoided that the optical axis of the sensor faces strong light sources such as sunlight and incandescent lamps. When the angle between the optical axis of the sensor (receiver) and the strong light source cannot be changed, a light-shielding plate or a long light-shielding tube can be installed around the sensor.
Mutual interference: MGK series of new photoelectric switches usually have the function of automatically preventing mutual interference, so there is no need to worry about mutual interference. However, when several groups of HGK series through-beam infrared photoelectric switches are installed in parallel and close to each other, they should prevent adjacent groups and mutual interference. The most effective way to prevent this kind of interference is to set the emitter and the receiver crosswise, and open the group distance when more than 2 groups. Different frequency models can also be used.
The effective way of HGK series reflective photoelectric switch to prevent mutual interference is to open the interval. And the farther the detection distance is, the larger the interval should be, and the specific interval should be determined according to the debugging situation. Of course, models with different operating frequencies can also be used.
Photoelectric switch wiring diagram:
The slot photoelectric switch is usually a standard U-shaped structure, and its transmitter and receiver are located on both sides of the U-shaped groove and form an optical axis. When the detected object passes through the U-shaped groove and blocks the optical axis, the photoelectric switch The detected switch signal is generated. The slot-type photoelectric switch is safe and reliable for detecting high-speed changes and distinguishing transparent and semi-transparent objects.
Optical fiber photoelectric switches use plastic or glass optical fiber sensors to guide light, so as to realize the detection that the detected object is not in the vicinity. Generally, fiber optic sensors are divided into through-beam type and diffuse reflection type.
related suggestion:
Photoelectric switch
Pepperl+Fuchs
liquid level sensor
Ultrasonic sensor
Surge protector
Safety barrier
Photoelectric switch articles:
Pepperl+Fuchs, as a pioneer in the field of sensor technology, continuously improves products and provides new applications in response to customer needs. Recently, Pepperl+Fuchs launched an innovative product-PMI inductive positioning system.
PMI inductive positioning system introduction:
This system has comprehensive functions, paving the way for modern Industry 4.0 applications: the positioning system is equipped with an IO-Link interface, which can be used for user-specific parameter settings, so users can detect and evaluate additional status information. PMI inductive positioning technology combines the robustness of inductive proximity sensors with the high precision of position measurement and angular positioning systems. The simple use of steel actuators is designed to maximize application flexibility. Pepperl+Fuchs continues to develop and improve this non-contact, wear-free technology. With the highest quality standards and the richest experience in the market, we provide a comprehensive inductive positioning system product line.
The advantages of PMI inductive positioning system at a glance
1. Adopt non-contact, maintenance-free technology and high environmental protection to ensure maximum durability
2. Using a simple steel actuator opens up various possible applications
3. Flexible with various functions, programmable measurement and switch range
4. Various shell designs: from compact machine tool design (14 mm measuring length) to heavy machine design (960 mm measuring length)
5. Strong anti-noise ability to ensure process reliability
6. Integration of measurement and switch functions to improve efficiency
PMI inductive positioning system is suitable for detecting linear position changes or measuring rotation angles. Reliable detection can be achieved even in dusty and oily environments or extreme temperature fluctuations.
Highest accuracy and maximum efficiency
The patented configuration and wiring of multiple coils in a single sensor, as well as intelligent evaluation, can achieve the highest accuracy and maximum efficiency. Using a simple steel actuator, whether the actuator is designed by the customer, a Pepperl+Fuchs proprietary accessory, or a part of the machine being inspected-PMI inductive positioning system can detect the precise position.
Use one sensor for measurement and switching functions
According to application requirements, only one sensor is needed to define the measuring range and multiple switching points or windows. The PMI sensor is used as a position sensor and limit switch at the same time. In other solutions that require multiple sensors, only one device is needed here.
Sensorik4.0®--paving the way for smart factories
The PMI induction positioning system is equipped with IO-Link, paving the way for the fourth industrial revolution. In the future of Industry 4.0 with a fully networked production system, sensors for communication play a vital role: send and receive sensor data during the production process, and receive higher-level local or cloud-based information systems.
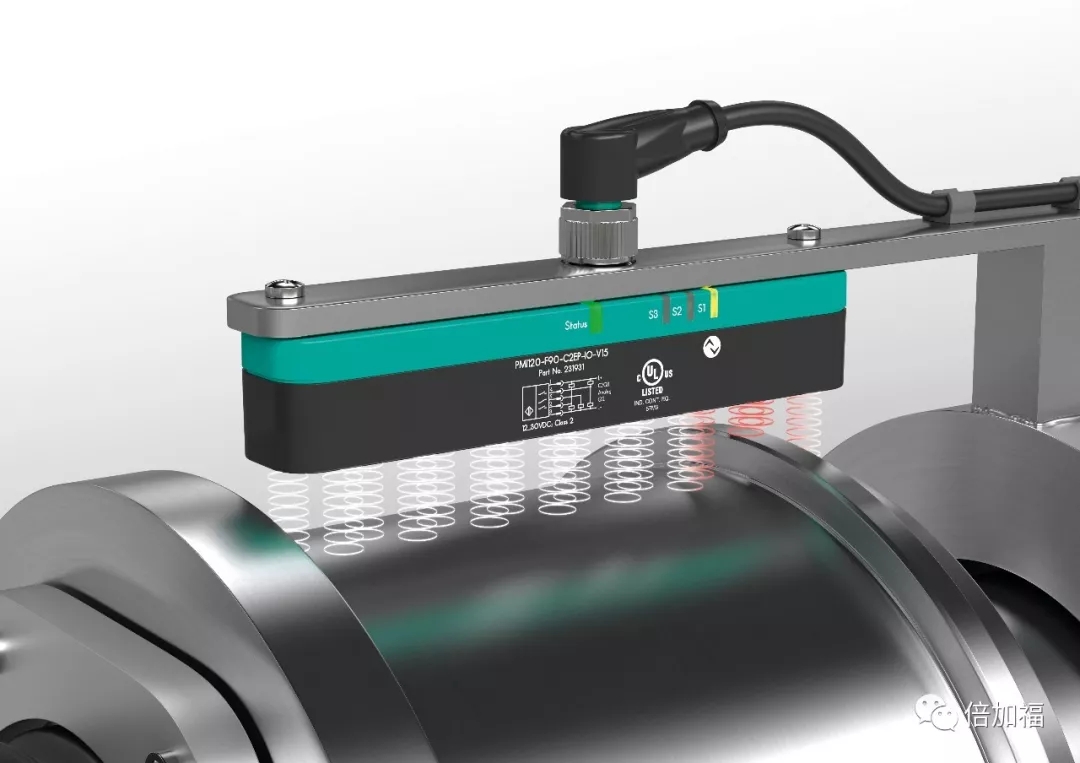
IO-Link opens up new possibilities
Direct communication at the sensor level/execution level, customized parameterization for customers and access to valuable additional information: the IO-Link interface opens up new possibilities for position detection. In addition to process data, value-added data such as signal quality or operating hours can also be accessed directly from the sensor.
With an accurate event log, you can determine how often the target leaves the measurement range and draw direct conclusions about mechanical tolerances, wear levels, or setup errors. In this way, event-oriented maintenance can be obtained-this concept is fully in line with Industry 4.0.
Paving the way for Industry 4.0, Pepperl+Fuchs is providing innovative sensor technology for Sensorik4.0®, using standard IO-Link interfaces to support the digitization of industrial applications.
Reliable process application examples
Control the guide roller system in the packaging machine, monitor whether the cylinder is clamped or provide valve position feedback in hazardous locations-the multifunctional F90 series is suitable for various applications.
Efficient guide roller control
In the winding and unwinding process in the packaging industry, the tearing or sagging of paper or film must be prevented. Guide rollers, known as "guide devices", are constantly adapted to the speed of machine operation to ensure reliable material feeding.
The F90 series reliably detects the position of the guide roller and realizes its own precise control. By combining measurement and switching functions in one device, two switching points or windows are also defined. In this way, not only the position of the guide roller can be used as an analog value, but also the position of two limit switches can be used as a switch signal from a single device. The guide roller system can be efficiently controlled without additional sensors.
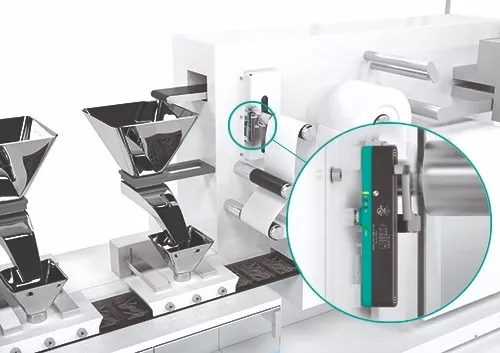
Safe use in hazardous locations
The F90 series can be quickly and easily installed on pneumatic diaphragm valves or linear control valves, and provide continuous position feedback, providing an ideal solution for precise valve position detection. The certified version makes the system suitable for hazardous locations in ATEX Zone 2/22 (3G nA, 3D tc).
The IP67 protection level and the rated temperature range of -25°C to +85°C ensure reliable use in outdoor environments.
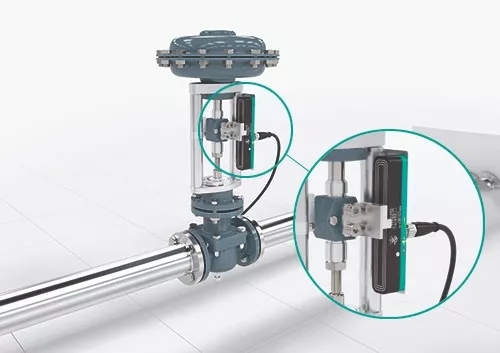