Rotary encoder installation matters
Rotary encoder installation matters
Rotary encoder is a kind of sensor that accurately measures angular displacement based on the principle of electromagnetic induction. There are windings in the rotor and stator. If a sinusoidal excitation current is passed through the rotor winding, the rotor induces a voltage of the same frequency in the stator winding, but the phase or amplitude changes with the relative displacement of the rotor and stator. The induced voltage is processed by electronic circuits such as A/D conversion by phase discrimination or amplitude discrimination, and outputs a number of digital signals (absolute value type), or outputs a multi-phase pulse or sinusoidal signal with a certain phase difference and frequency difference. Generally speaking, rotary encoders include incremental rotary encoders, absolute rotary encoders, sinusoidal output rotary encoders, and motor rotary encoders! Generally, many advanced coal mines have applications when PLC systems are used for the control of underground motors.
Notes for the application of rotary encoder (three parameters should be noted):
1. Mechanical installation dimensions, including positioning stop, shaft diameter, installation hole position; cable outlet method; installation space volume; whether the working environment protection level meets the requirements.
2. Resolution, that is, the number of pulses output per revolution when the encoder is working, and whether it meets the design and use accuracy requirements.
3.Electrical interface, encoder output methods commonly include push-pull output (F type HTL format), voltage output (E), open collector (C, common C is NPN type tube output, C2 is PNP type tube output), long line driver Output. Its output mode should match the interface circuit of its control system.
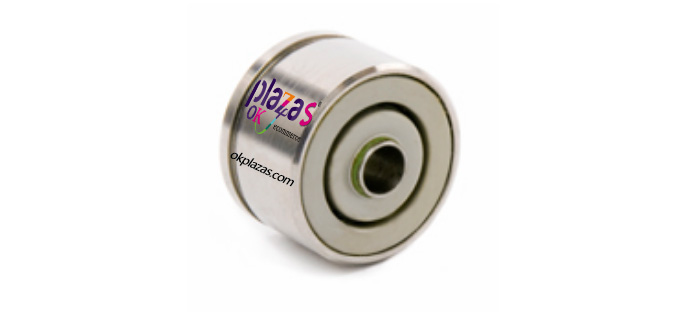
Rotary encoder installation steps
1. Please install your encoder firmly to avoid vibration and looseness.
2. When the encoder shaft and the machine shaft are connected, please make sure that the load of the shaft cannot exceed its maximum allowable value.
3. When the shaft of the encoder is connected to the shaft of the machine through the coupling, please make sure that there is no deviation.
4. Please do not connect with rigid coupling.
5. Please tighten the screws of the coupling to avoid loosening during use.
6. Please choose a suitable coupling, because the weight of the coupling also increases the load of the shaft.
7. When connecting with a conveyor belt, please use a timing conveyor belt, otherwise the transmission angle is not accurate.
8. When using timing belts, make sure that the belt tension is appropriate. Please pay attention to belt installation and loosening during use.
9. Please avoid the vibration and deviation of the pulley caused by the radial load during the rotation.
10. When the shaft of the encoder and the shaft of the machine are connected by gears, please avoid the part or the whole of the gear from being vibrated by the radial load.
11. Please do not knock the encoder through couplings, conveyor belts and gears.