What are the classifications of encoders
What are the classifications of encoders
The photoelectric encoder applies the photoelectric conversion principle, which can convert the mechanical geometric displacement on the output shaft into pulse or digital quantity. This is the purpose
The most used sensor in the past, because the photoelectric code disc is coaxial with the motor, when the motor rotates, the code disc (grating disc) and the motor are at the same speed
Rotation reflects the current motor speed.
It is mainly composed of 4 parts: light source, code disc, optical system and circuit. Then we will explain according to different types of photoelectric encoders.
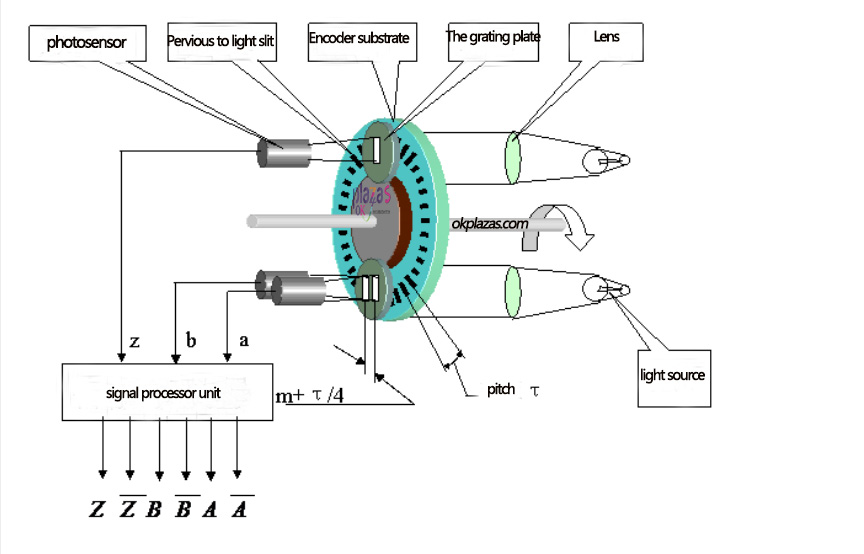
1. Incremental encoder
It can convert the displacement into a periodic electrical signal, and then convert this electrical signal into a count pulse, and rotate the incremental encoder to rotate
Output pulse when moving, and know its position by counting device. And the position is the number of pulses counted from the zero mark is OK
Yes, after a power failure, the encoder cannot move anymore. When the power is turned on again, the encoder cannot interfere with the output pulse.
Disturbance and loss of pulse, otherwise, the zero point memorized by the counting device will shift. Wrong results are difficult to find, such as unable to accurately locate the reference
Point, the accuracy of the location cannot be guaranteed. Therefore, you must first find the reference point for each operation. But such an encoder is not affected by power outages and interference.
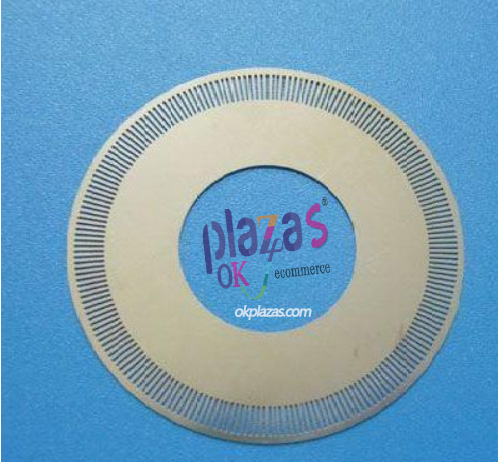
Incremental encoders can use the principle of photoelectric conversion to output three groups of square wave pulses A, B and Z; A and B pulses have a phase difference of 90 degrees, which can be judged
The rotation direction of the motor is cut off, and the Z-phase outputs a pulse for each revolution for reference point positioning. The principle structure of this encoder is simple
Single, mechanically average, and the service life can reach tens of thousands of hours, with strong anti-interference ability and high reliability. But it cannot output shaft rotation
Move the absolute position information.
2. Absolute encoder
Each position of the absolute encoder corresponds to a certain digital code, so its indication is only related to the start and end positions of the measurement.
It has nothing to do with the intermediate process of measurement. Its position is determined by the reading of the output code. When the power is disconnected, the absolute encoder is not separated from the actual position. When the power is turned on again, the position reading is still current
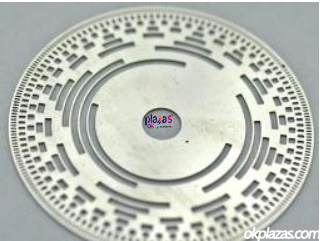
Absolute encoders can directly output large digital quantities. There will be several code channels on the code disc, and the number of code channels is the binary digit. Each bar code track is composed of light-transmissive and opaque fan-shaped areas, and signals are collected by using photoelectric sensors. A light source and a photosensitive element are respectively arranged on the side of the code disc, so that the photosensitive element can perform level conversion according to whether or not the light signal is received, and output a binary number. And output different digital codes in different positions. Thus, the absolute position can be detected. But the resolution is determined by the number of bits in the binary, which means that the accuracy depends on the number of bits. Advantages: The absolute value of the angle coordinates can be read directly, there is no cumulative error, and the position information will not be lost after the power is cut off. The anti-interference characteristics of the encoder and the reliability of data are greatly improved.
Three, hybrid absolute encoder
Hybrid absolute value encoder, it outputs two sets of information: one set of information is used to detect magnetic pole position, with absolute information function; the other set
It is exactly the same as the output information of the incremental encoder.
Four, resolver
The resolver is abbreviated as resolver. It is composed of high-performance silicon steel laminates and enameled wires with a special electromagnetic design. Compared with the encoder using photoelectric technology, it has heat resistance and vibration resistance. Adaptability to harsh working environments such as impact resistance, oil stain resistance, and even corrosion resistance.
A pair of poles (single speed) resolver can be regarded as a single-turn absolute feedback system, which is also the most widely used.
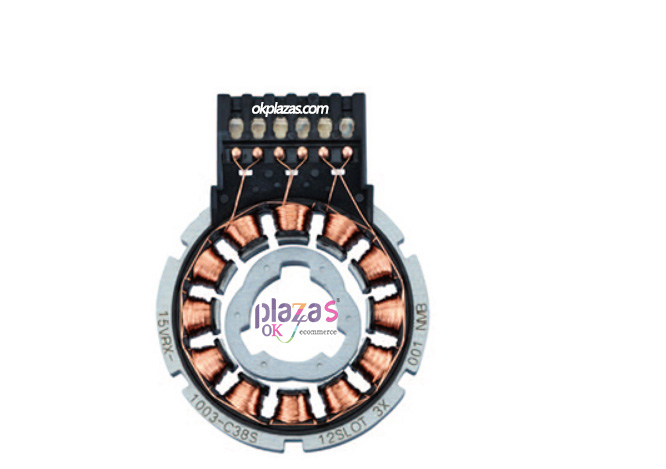
Five, sine cosine servo motor encoder
The servo drive can obtain high-precision subdivision without high-frequency communication, which reduces the hardware requirements. At the same time, because of the single-turn angle signal, the servo motor can start smoothly and have a large starting torque.
In order to be able to better test the performance parameters of the motor, the MPT motor test system of ZLG Zhiyuan Electronics Co., Ltd. created the original "free loading engine" technology, which can perform control response testing and step response testing. It can meet the transient measurement needs of motors and drives and promote the development of the industry.