What is the principle of rotary encoder
What is the principle of rotary encoder
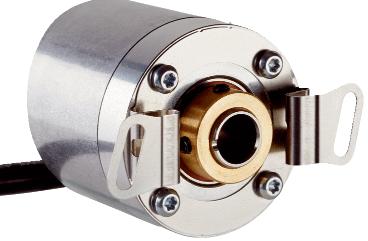
2.1 Photoelectric encoder
Photoelectric encoder: It is a kind of sensor that converts the mechanical geometric displacement on the output shaft into pulse or digital quantity through photoelectric conversion. This is the most widely used sensor at present. The photoelectric encoder is composed of a grating disc and a photoelectric detection device. The grating disc is a circular plate with a certain diameter and a number of rectangular holes are equally opened. Since the photoelectric code disc is coaxial with the motor, when the motor rotates, the grating disc rotates at the same speed as the motor, and a detection device composed of light-emitting diodes and other electronic components detects and outputs several pulse signals.
Advantages: small size, precision, high resolution, no contact and no wear; the same type can detect angular displacement and linear displacement with the help of mechanical conversion device; domestic single-turn absolute encoder can do 8- 24-bit resolution, accuracy to ±2", multi-turn photoelectric absolute encoder can detect a fairly long linear displacement (such as 25-bit multi-turn), incremental encoder can reach the highest direct engraving 18000 line resolution; long life , The installation is free, the interface is rich, the price is reasonable; the technology is mature, and it has been widely used at home and abroad many years ago.
Disadvantages: Conventional products have high precision, but high requirements for outdoor and harsh environments.
2.2 Magnetoelectric encoder
Magnetoelectric encoder is a new type of angle or displacement measuring device, its principle is to use magnetoresistance or Hall element to measure the angle or displacement value of changing magnetic materials. The change of the angle or displacement of the magnetic material will cause a certain resistance or voltage change. The change is amplified by the amplifying circuit, and the pulse signal or analog signal is output after processing by the single-chip microcomputer to achieve the purpose of measurement. Its structure is divided into two parts: sampling detection and amplifying output. The detection is generally completed by a bridge circuit, and there are two types of half bridge and full bridge. Amplified output is generally realized through devices such as transistors and operational amplifiers.
Advantages: The magnetoelectric encoder has the characteristics of anti-vibration, anti-corrosion, anti-pollution and wide temperature.
Disadvantages: low resolution; poor anti-interference performance. Existing absolute encoders on the market can only do 12 bits, and incremental encoders can only do 2048 resolution. High resolution needs to be subdivided.
okplazas.com has a wide range of encoder types, high resolution, support for customized high precision, high protection level, low temperature absolute encoder, support
RS485, RS422, RS232, SSI. CANOPEN, BISS and other interfaces. Please contact us for the purchase of encoder products.
Consulting Hotline: +86-13689242098